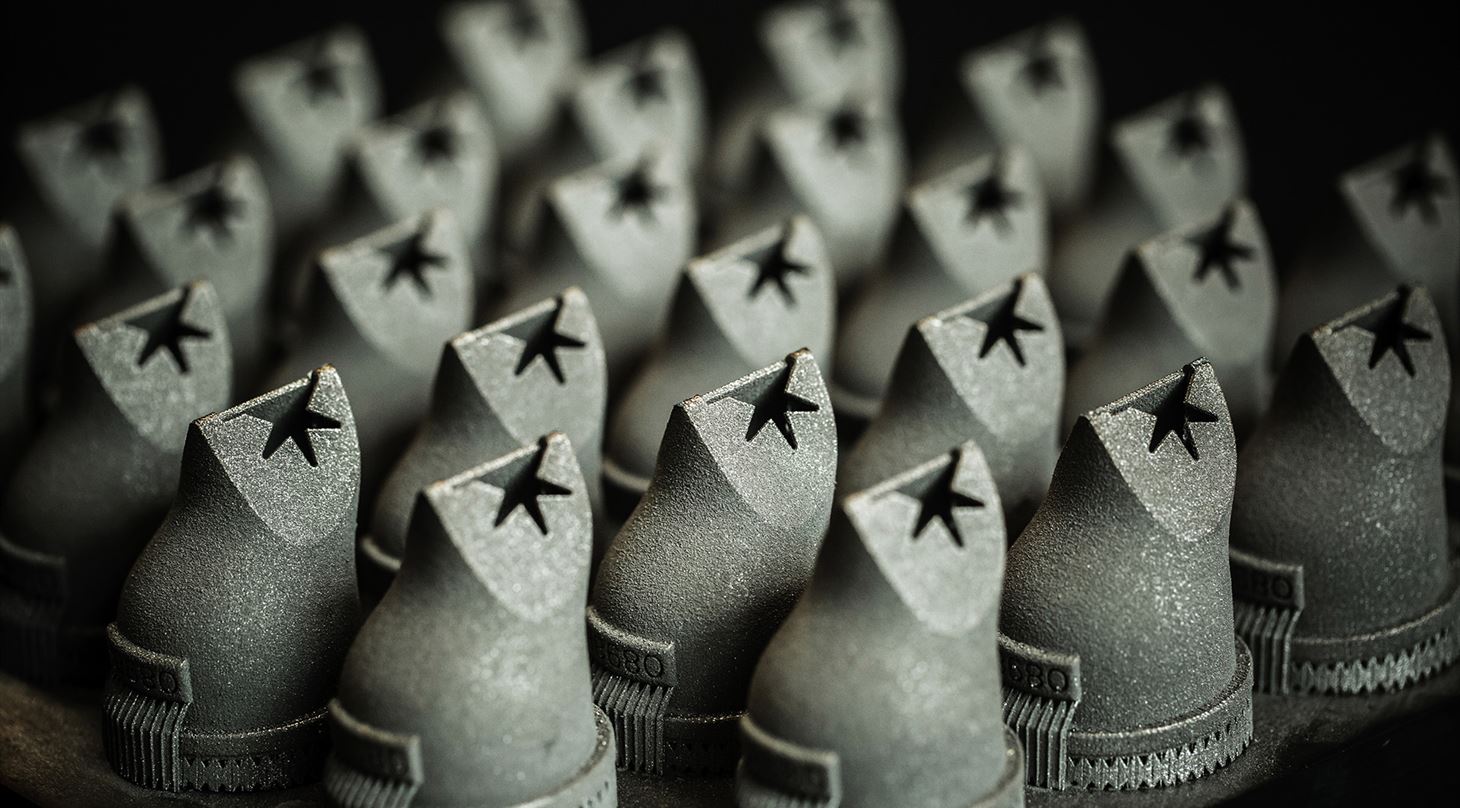
Designfrihed og hurtig produktion fik Bühler Meincke til at satse på metal 3D-print
Bühler Meincke opdagede 3D-print, da de stod med nogle emner, hvor de ikke kunne opnå den ønskede geometri med traditionelle fremstillingsmetoder. Teknologien gav dem en enorm designfrihed, og sidenhen tog de skridtet til metal 3D-print, som i første omgang blev brugt til virksomhedens småkagetyller. I dag bruges metal 3D-print til serieproduktion af flere forskellige emner, som bliver fremstillet på Teknologisk Institut.
Bühler Meincke udvikler og producerer maskiner til småkage- og kikseproduktion verden over, og deres rejse med 3D-print startede, da de havde brug for nogle specielle geometrier til småkagetyller. Traditionelle fremstillingsmetoder viste sig at komme til kort, og derfor undersøgte de forskellige muligheder og fandt i den forbindelse frem til 3D-print i plast, som gav en enorm designfrihed.
Lad os hjælpe dig med produktion af 3D-print
Det blev starten på en ny æra for Bühler Meincke, som for nogle år siden tog springet videre til metal 3D-print, hvor de kunne opnå den samme designfrihed med en væsentlig større holdbarhed - og ikke mindst i materialer, der er godkendt til fødevarekontakt.
Afsæt i MADE demonstrationsprojekt
Opstarten med metal 3D-print skete i et demonstrationsprojekt fra MADE - Manufacturing Academy of Denmark i 2017, hvor Bühler Meincke undersøgte mulighederne for at implementere 3D-printede metalemner i produktionen. Det skete med hjælp fra Teknologisk Institut, som har fire metalprintere i Center for industriel 3D-print.
MADE demonstrationsprojektet fokuserede på de små tyller, som giver småkagerne den ønskede form, når dejen presses igennem. Til disse tyller havde Bühler Meincke brug for et hygiejnisk design med organiske former, og derfor var 3D-print et oplagt match.
- Tidligere blev tyllerne loddet sammen af flere dele, da formen ikke kunne opnås med fræsning. Det var et kompliceret og tidskrævende arbejde, som samtidig gav nogle uønskede samlinger, hvor bakterier kunne ophobe sig. Desuden havde Bühler Meincke kun én mand ansat til at udføre dette arbejde, så de var enormt afhængige af denne person. Men med 3D-print blev det muligt at lave tyllerne i ét stykke, som får en glat og rengøringsvenlig overflade, siger Kristian Rand Henriksen, Forretningsleder ved Teknologisk Institut.
Se filmen om Bühler Meinckes tyller herunder:
Ydermere bliver reproducerbarheden af tyllerne højere med 3D-print, og produktionsprocessen bliver forenklet og mere personuafhængig.
- Tyllerne blev bedre, end jeg overhovedet havde forestillet mig, da vi startede, og vi er jo så langt, at vi allerede kan bruge det i vores produktion. Og derudover er der mange andre emner, der har potentiale for at blive fremstillet med 3D-print, lød det fra Per Bjerrum, Technology Expert hos Bühler Meincke umiddelbart efter demonstrationsprojektet.
Teknologisk Institut 3D-printede tyllerne i rustfrit stål 316L og titanium til Bühler Meincke, og projektet gik over al forventning – faktisk så godt, at Bühler Meincke i dag får produceret største delen af deres tyller med 3D-print hos Teknologisk Institut. En anden væsentlig detalje ved de 3D-printede tyller er, at både rustfrit stål og titanium er godkendte fødevarekontaktmaterialer – noget der var et krav fra Bühler Meinckes side - og Teknologisk Institut har komplet sporbarhed på hvert printet emne hele vejen gennem produktionen.
- Demonstrationsprojektet har vist, at metal 3D-print er specielt interessant for fødevarebranchen. Det kan være virksomheder, som fremstiller bageriprodukter, iscreme eller mejeriprodukter, men teknologien er også interessant for farmaceutiske virksomheder og for producenter af piller og medicinsk udstyr, siger Mads Østergaard, sektionsleder og 3D-print ekspert på Teknologisk Institut.
Øget fokus på 3D-print i produktionen
I kølvandet på MADE demonstrationsprojektet, er Bühler Meincke gået videre med 3D-print i metal. Det skyldes ikke mindst designfriheden, som gør, at de kan være langt mere fri i deres tankegang og lave mange flere faconer, som ikke kan lade sig gøre med traditionel fremstilling.
- Takket være designfriheden med 3D-print har vi kunnet løse nogle af udfordringerne med organisk og hygiejnisk design, hvor vi nu kan slippe af med samlingerne og hjørnerne fra traditionel fremstilling. Desuden var selve fremstillingen af tyllerne tidligere en kompleks affære, men med 3D-print sender vi bare en STEP-fil til Teknologisk Institut, som så klarer produktionen – og så er det pludselig temmelig let for os, lyder det fra Kennie Larsen, Head of Cookie Feed & Forming hos Bühler Meincke.
Efterfølgende har Bühler Meincke kigget på flere emner i produktionen, som kunne optimeres med 3D-print. Det kunne fx være emner, som ville kunne laves bedre, billigere eller mere vægtoptimerede - og resultaterne har været positive. Bl.a. er man begyndt at 3D-printe en såkaldt cutter-roller, som tidligere var et rør, hvorpå der blev svejset fx seks kopper til at udstikke dejen.
Nu laver vi cutter-rolleren direkte i 3D-print, og det er faktisk langt bedre end traditionel fremstilling, for når du svejser har du meget varme, og emnerne deformerer, men 3D-print har vist sig at kunne løse disse udfordringer
- Kennie Larsen, Bühler Meincke
Også fremadrettet ser Bühler Meincke et stort potentiale i 3D-print. Indtil nu har man primært fokuseret på mindre emner – også fordi der er nogle begrænsninger på, hvor store emner, man kan printe. Men der er et ønske om at være up-to-date med teknologien, så man er klar til at drage fordel af de nye muligheder, i takt med at de opstår.
Et nyt værktøj i kassen – med kort leveringstid
I dag tænker Bühler Meincke 3D-print ind som fremstillingsmetode på lige fod med mere traditionelle metoder, da de kan se potentialet i teknologien, og da den giver en række nye muligheder, som de ikke havde før. Ud over designfrihed er der således også kort leveringstid på de 3D-printede emner, som samtidig kan fås i de ønskede materialer – rustfrit stål og titanium. Og så oplever Bühler Meincke især en fordel ved metal 3D-print i prototypefasen samt i overgangen fra prototype til slutprodukt.
- Det er let og hurtigt at producere en part, som kan testes direkte i maskinerne, så man kan se, om det hele virker. Herefter er det den samme kvalitet, vi får i slutproduktionen, så vi skal ikke teste med 3D-print for herefter at producere på anden vis – vi tester faktisk det færdige produkt, som det kommer til at se ud, og det er en kæmpe fordel, lyder det fra Kennie Larsen.
Samarbejdet med Teknologisk Institut får også rosende ord med på vejen. Ud over 3D-print produktion bruger Bühler Meincke også instituttet til test og løbende sparring omkring mulighederne med 3D-print.
- Når vi har fælles workshops, har Teknologisk Institut været rigtig gode til efterfølgende at teste mulighederne med vores produkter for at se, hvad der kan lade sig gøre. På den måde arbejder vi sammen om at finde ud af, om der skulle være et uopdaget potentiale for 3D-print blandt vores komponenter, slutter Kennie Larsen
Fakta:
Bühler Meincke er en del af Bühler Group, som er en global producent af bl.a. anlæg og udstyr til behandling af fødevarer. Virksomheden har hovedsæde i Schweiz, og i Skovlunde, Danmark laver man udstyr til småkager og kager - det er hertil, at Teknologisk Institut 3D-printer bl.a. småkagetyller og cutter rollers i titanium og rustfrit stål.