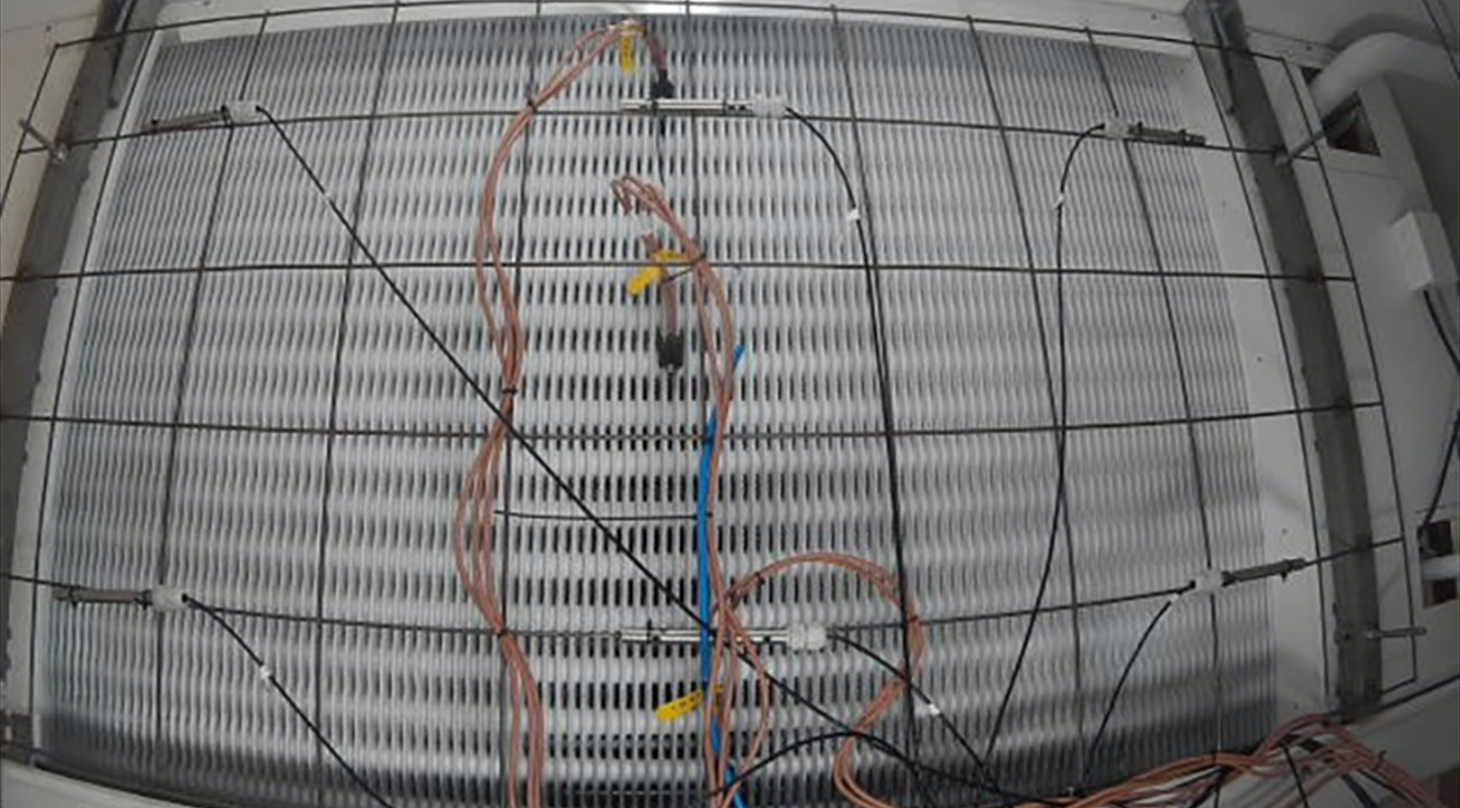
Nu skal fyldningerne sænkes på industrielle ammoniakkølesystemer – og effektiviteten forbedres
Fremtidssikring af det mest effektive kølemiddel til det industrielle marked. Ammoniak har fortrinlige termodynamiske egenskaber og anvendes i langt de fleste industrielle køle- og fryseinstallationer verden over. De industrielle ammoniakkøleanlæg, der designes i dag, indeholder dog betydelige mængder kølemiddel og kan gøres langt mere energieffektive. Netop nu leder Teknologisk Institut et projekt, der handler om at udvikle industrielle ammoniakkølesystemer med en forbedret energieffektivitet og lavere fyldninger, som kan modstå konkurrencen fra andre mindre effektive alternative løsninger.
Ammoniak anvendes som kølemiddel i størstedelen af alle industrielle køle- og fryseinstallationer verden over. Og dansk industri er førende på området. Ikke blot direkte i form af køleindustrien, men også gennem de store industrier inden for maskinleverancer til fødevareindustrien, hvor køletekniske installationer spiller en helt central rolle.
I et nyt projekt arbejder Teknologisk Institut på at udvikle nye systemløsninger, der skal nedbringe energiforbruget i industrielle køleanlæg med ammoniak. Samtidig skal løsningerne også imødekomme en ny global trend, der handler om at øge anlæggenes sikkerhed ved at sænke kølemiddelfyldningerne i anlæggene væsentligt. Udviklingsarbejdet vil sikre, at dansk industri også fremover kan tilbyde sikre ammoniakkøleanlæg med den højeste energieffektivitet samlet set.
De traditionelle anlæg
Traditionelt bygges industrielle ammoniakanlæg som oversvømmede – dvs. med overcirkulation igennem fordamperen – da det giver en mere effektiv drift af selve fordamperen. Men det medfører også et højere tryktab fra fordamperen frem til kompressoren, idet der skal trækkes væske med retur fra fordamperen – med et betydeligt ekstra elforbrug til følge.
I anlæg, hvor der bruges andre kølemidler end ammoniak, anvender man som regel direkte ekspansion (DX). Denne teknologi medfører normalt også store tab pga. kravet om overhedning – også her med et betydeligt ekstra elforbrug til følge. Til gengæld giver teknologien mulighed for både enklere og billigere anlægsinstallationer. DX-teknologien har dog aldrig for alvor vundet indpas i industrielle ammoniakanlæg, da den er svær at styre pga. den ekstremt høje latente varme, som ammoniak har – og dermed lave massestrøm. Vand og olie, som altid er indeholdt i industrielle ammoniakkøleanlæg, giver også ekstra udfordringer, når DX-teknologien bruges til fordamperne. Især vand – selv i små mængder – giver store problemer.
Design af nye løsninger
Til forskel fra de traditionelle anlæg skal der i de nye løsninger udvikles komponenter, der kan styre de traditionelle anlæg hen imod et lavere energiforbrug og lavere fyldningsmængder. Tryktabet skal minimeres ved, at der udvikles en kontinuerlig aktiv styring og kontrol, der sikrer drift ved minimal cirkulation igennem selve fordamperen samt mindsker eller eliminerer behovet for at trække væske retur. Denne aktive styring vil minimere de energitab, der findes i de anlægsløsninger, der anvendes i dag.
Der skal udvikles to metoder. Den ene metode kaldes CCR (Controlled Circulation Rate). Her er cirkulationen igennem fordamperen indstillet til den lavest mulige, og den holdes der under forskellige belastningsvariationer. På den måde spares der energi pga. et mindre tryktab i returrørene, og fyldningen sænkes pga. mindre cirkulation i rørsystemet. Denne metode udvikles til allerede eksisterende fordampere.
Den anden metode kaldes DR (Dry Return). Her skal der udvikles udstyr, således at gassen, der kommer ud fra fordamperen, er tør, men uden overhedning. På den måde er det muligt at gøre anlæggene væsentligt billigere og enklere og på samme tid forbedre effektiviteten i forhold til eksisterende løsninger.
For yderligere at øge effektiviteten og mindske fyldningerne på fordamperne skal brugen af microchannel-profiler til fordampere undersøges. De udfordringer, der vil blive kigget på, er tilrimning og efterfølgende afrimning af fordamperne. Derudover vil vi også kigge på, hvilken indflydelse olie og vand har på fordamperen.
Markant reduktion af energiforbrug
Jóhannes Kristófersson, seniorprojektleder i Center for Køle- og Varmepumpeteknik på Teknologisk Institut, har høje forventninger til de nye systemløsninger:
”En konservativ forventning til de nye løsninger er en elbesparelse – alene i Danmark – på 15 GWh om året. Og eftersom industriel køling bruges i næsten alle fødevareproduktionsfirmaer i verden, forventes potentialet at være endnu større, hvis det lykkes at udbrede teknologien globalt. Hertil kommer en tilsvarende vækst hos de virksomheder, som kan anvende de udviklede teknologier i deres produkter”.
Du kan løbende følge projektet her
Vil du vide mere, så kontakt Jóhannes Kristófersson på tlf.: 72 20 32 54 eller via e-mail: jkri@teknologisk.dk.
Om projektet
I projektet, som løber over de næste tre år, samarbejder Teknologisk Institut med Danfoss, DTU, Innoterm, Aluventa, Scanico og Claus Sørensen.
Projektet er støttet af EUDP.