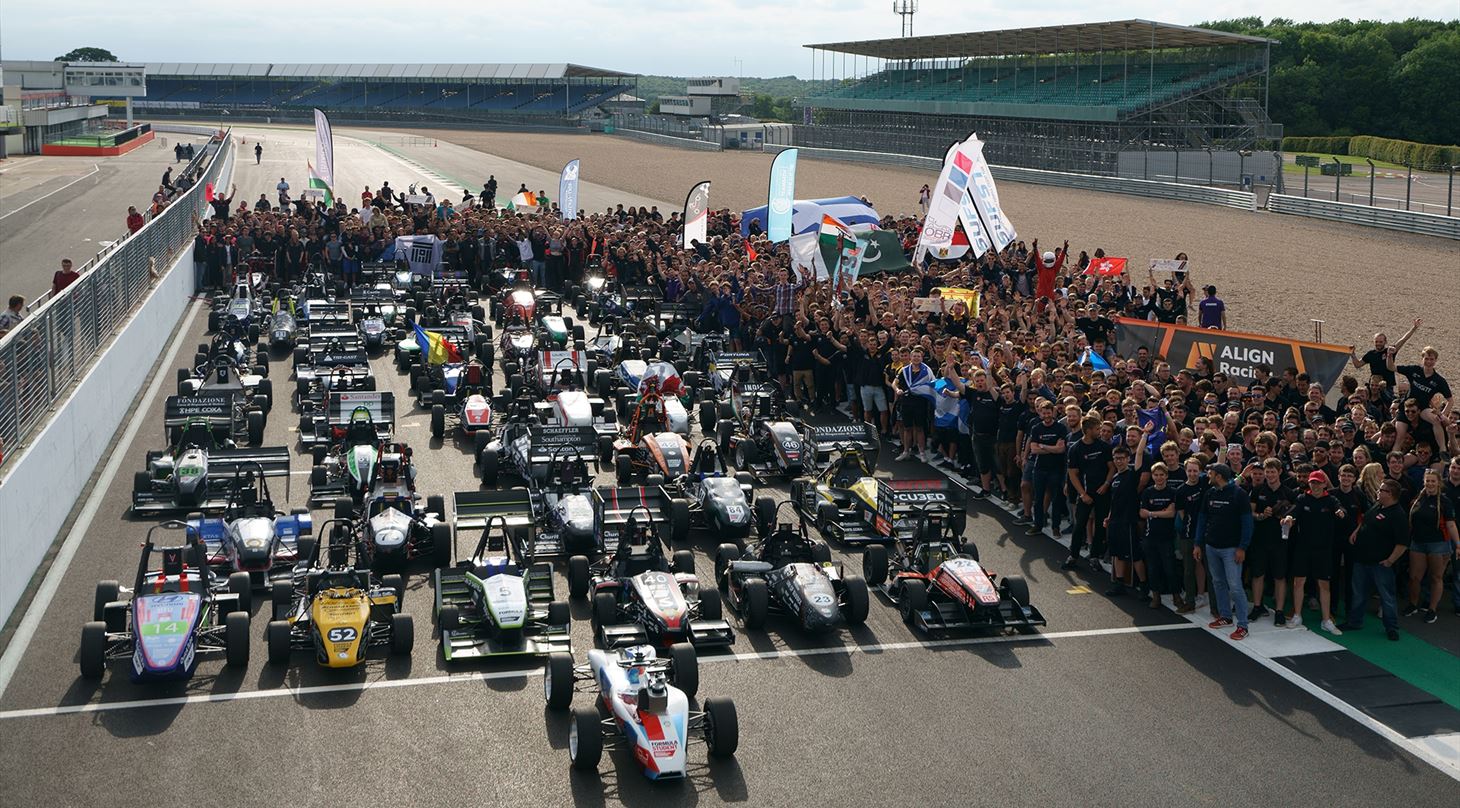
3D-metalprint gav designfrihed til racerbils hjulophæng
Teknologisk Institut har 3D-printet en del af hjulophænget til den racerbil, som ingeniørstuderende på Syddansk Universitet har med i Formula Student projektet, hvor de konkurrerer mod studerende fra 5-600 universiteter verden over. Hjulophænget blev printet i titanium, og 3D-print gav en større designfrihed, som løste en række geometriske og bearbejdningsmæssige udfordringer.
Teknologisk Institut blev kontaktet af ingeniørstuderende fra Syddansk Universitet, som I forbindelse med Formula Student-projektet havde et ønske om at arbejde med 3D-print til hjulophænget på den racerbil, de skulle bygge. De studerende havde oplevet udfordringer med den del af hjulophænget, hvor bærekuglerne skulle presses i, og efter at have set en artikel om 3D-print, så de både en anledning til at stifte bekendtskab med 3D-print som produktionsteknologi og samtidig få løst udfordringerne.
Lad os hjælpe dig med produktion af 3D-print
- 3D-print kom ind i billedet til vores hjulophæng, fordi geometrien til endestykkerne, som vi limer ind i vores kulfiberrør, var besværlige at bearbejde på med fx CNC-maskiner, men det problem blev løst med 3D-print. Samtidig gav teknologien os mulighed for at løse nogle af de udfordringer, vi oplevede, når vi limede et endestykke i hver ende af kulfiberrørene. Med 3D-print kunne vi nemlig lave nogle interne kanaler, som overtrykket kunne ledes ud igennem, og dermed undgik vi, at limen blev presset væk fra limfladerne, fortæller Kevin Evardsen Grau, civilingeniør-studerende på Syddansk Universitet og en del af Formula Student-projektet.
I processen har de studerende leveret tegninger til de 3D-printede emner, og de har designet emnerne både til brugskontektsten og fremstillingsprocessen. Undervejs har de sparret med Teknologisk Instituts eksperter omkring bl.a. materialeegenskaber og enkelte designelementer såsom ringene omkring lejerne – og så har de lavet det færdige design ud fra disse input. Valget af materiale faldt på titanium, da det er et let, stærkt og stift materiale, som dermed passede til kravene.
Teknologisk Institut har et ønske om at udbrede kendskabet til 3D-print i metal, og det var en af grundene til, at man valgte at gå ind i Formula Student-projektet – derfor har det også været positivt at se, hvordan de studerende udnyttede mulighederne ved 3D-print teknologien.
- Vi har valgt at støtte op om Formula Student-projektet, fordi vi gerne vil introducere de studerende til 3D-metalprint og give dem hands-on erfaring med teknologien. Og så vil vi gerne vise, at Teknologisk Institut er en tilgængelig samarbejdspartner, ikke bare for SMV’er og større virksomheder, men også for studerende, fortæller Mads Østergaard, faglig leder på Teknologisk Institut.
Designfrihed gav flere muligheder
I arbejdet med 3D-print har de studerende udnyttet designfriheden – fx i forhold til, at de printede emner skal forbindes med kulfiberstænger, som giver afstanden på hjulophænget. Når metal og kulfiber skal samles, har man brug for noget, som kulfiberen kan gribe fat i. Her har man en god stor limoverflade, hvor overfladeegenskaberne fra 3D-printet er meget velegnede, Så emnet er optimeret til 3D-print ved samlingerne, og med denne optimering, ville det blive alt for dyrt at bearbejde dem i forhold til at 3D-printe.
De 3D-printede titaniumemner har fået standard efterbearbejdning på Teknologisk Institut, og efterfølgende har de studerende limet emnerne sammen med kulfiberstængerne. Det er nemlig en væsentlig del af projektet, at de studerende selv skal designe og samle bilen. Dog må de gerne få enkelte dele fra eksterne leverandører, og her har 3D-print været lidt af en øjenåbner.
- Det har været superspændende at arbejde med 3D-print i metal, i det her tilfælde titanium, fordi man kan printe i så høj styrke, som man kan. Det er også lidt sjovt at opleve, hvordan hjernen pludselig kan være den begrænsende faktor, fordi man tænker i de her traditionelle bearbejdningsmetoder, lyder det fra Andreas S. Mehl, Adjunkt på Syddansk Universitet og mekanisk vejleder for SDU-Vikings, som er navnet på det hold, der deltager i Formula Student-projektet.
3D-print håndterer ekstrem belastning
For Teknologisk Institut har opgaven været spændende, fordi der med racerbiler er tale om et high-end område, hvor emnerne bliver udsat for nogle ekstreme belastninger, og hvor man ikke nødvendigvis kan beregne sig til, hvordan de vil reagere – det hænger bl.a. også sammen med, hvordan bilen bliver kørt. Derfor ligger der en interessant læring i at finde ud af, hvor langt man kan gå ned i vægt og stadig bevare holdbarheden – og vel at mærke på et emne, som er optimeret til det, det skal bruges til, og hvor der ligger en række beregninger bag.
Se hvordan vi kan hjælpe dig med 3D-print
For at undersøge, om de 3D-printede emner kunne holde til brugen, blev der først printet demoemner, som de studerende lavede træktest på, hvor emnet blev trukket i stykker. Her skete bruddet præcist der, hvor simuleringen og FEM-beregningen havde forudset det, og da man således var sikker på, at emnerne kunne holde, blev de færdige emner 3D-printet, så de passede til de forskellige monteringer i hhv. højre og venstre side på forhjul og baghjul.
Se en video om samarbejdet mellem Formula STudent og Teknologisk Institut - artiklen fortsætter under videoen.
Stor fremtidigt potentiale for 3D-print
Formula Student-projektet kører videre på Syddansk Universitet næste år med nye studerende, og her kan den eksisterende bil enten videreudvikles eller danne erfaringsgrundlag for konstruktionen af en endnu bedre bil.
I den forbindelse har folkene omkring projektet allerede flere ideer til, hvor og hvordan 3D-print kan bruges. En af mulighederne er at optimere hjulenes nav – de såkaldte upright hub assemblies. I dag er de bearbejdet ud af en klump aluminium, og der kunne man topologi optimere, hvor man fjerner unødvendigt materiale, så man får hulrum og en mere ’knogle-lignende’ struktur. På den måde kan man spare en masse vægt på den uaffjedrede masse, som har stor indflydelse på de omgangstider, som bilen kan præstere. Og fordi de studerende allerede har testet de nuværende emner og set, at deres beregninger stemmer overens med testresultaterne, er der stor sandsynlighed for, at fremtidige topologioptimerede emner vil kunne klare de belastninger, de udsættes for.
- Det er oplagt at bruge 3D-print i Formula Student, også i fremtiden. Vi bygger prototyper, der skal være lette, så vi kan komme hurtigst muligt rundt på racerbanen, og det er jo også derfor, at vi ser 3D-printteknologien anvendt i Formel 1, slutter Andreas S. Mehl.
I næste step kan der også blive tale om at 3D-printe andre komponenter på bilen, da der er potentiale for yderligere optimering – og den skal de studerende forsøge at opnå. Målet med konkurrencen er nemlig ikke bare at være med i konkurrencen – de studerende skal også lære noget om de forskellige fremstillingsprocesser, så de udvider deres kompetence-palet, og udviklingen peger på, at 3D-print bliver en endnu vigtigere del af værktøjskassen i fremtiden.
Fakta om Formula Student
Formula Student går ud på, at ingeniørstuderende fra 5-600 universiteter på verdensplan konkurrerer om at bygge den bedste racerbil. Konkurrencen afholdes hvert år, og de studerende designer, bygger, tester og kører bilen, og der køres løb på racerbaner rundt omkring i Europa. Konkurrencen er inddelt i statiske og dynamiske test, så der både skeles til bilens design og dens køreegenskaber. Fra Syddansk Universitet deltager SDU-Vikings Racing Team, som er et af fire hold i Danmark.