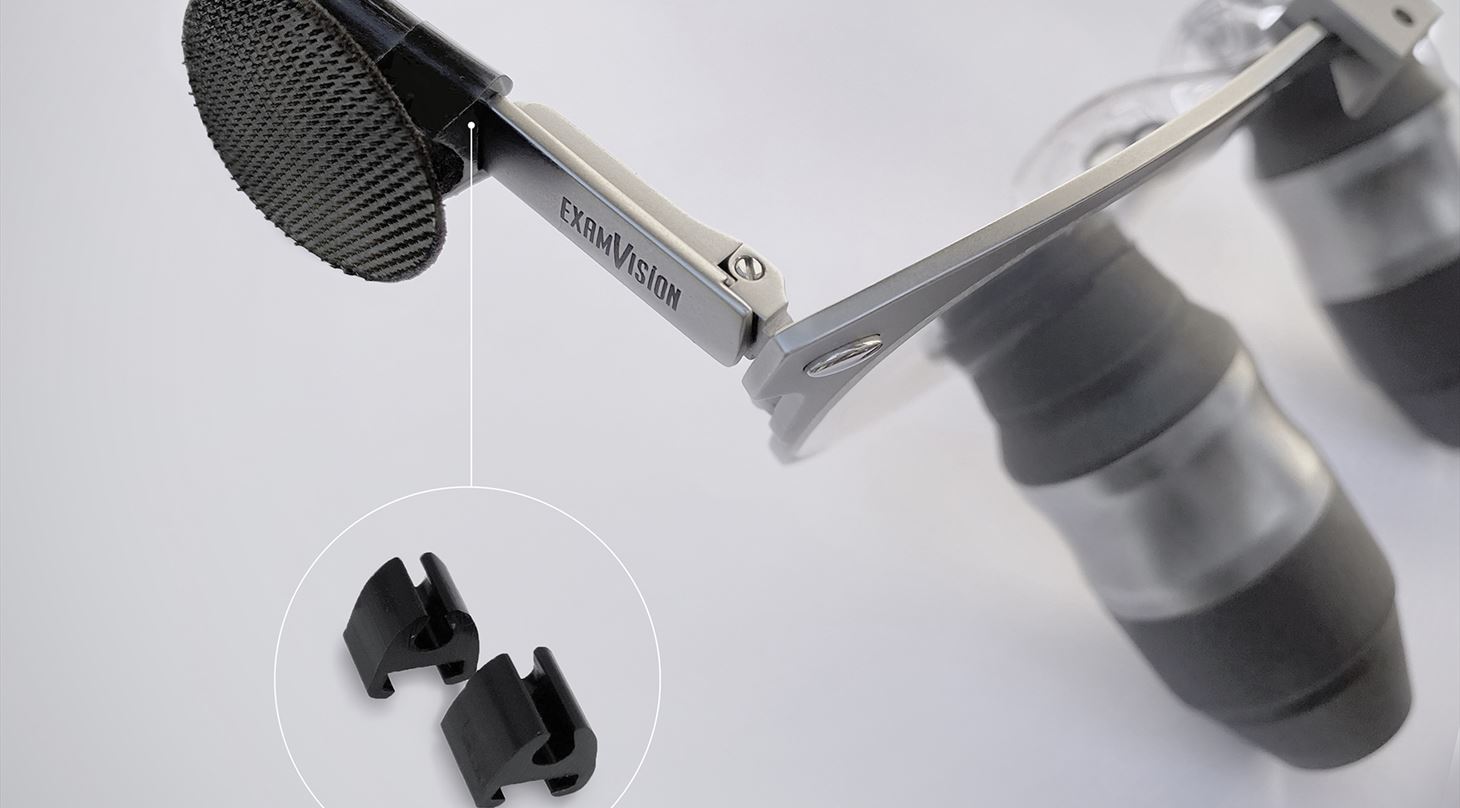
3D-print løste ExamVisions akutte behov for visirholdere
Den danske virksomhed ExamVision fra Samsø laver lupbriller, som læger og tandlæger over hele verden benytter ved behandlinger og operationer. Efter den første COVID-19 bølge oplevede ExamVision en kæmpe efterspørgsel og en ny udfordring, da aflyste behandlinger blev genoptaget – nu med krav om ansigtsvisir – men med 3D-print var man i stand til at imødekomme det akutte behov.
Når danske ExamVisions laver lupbriller til tandlæger og kirurger, er brillerne 100% skræddersyede til den enkelte læges fysik, syn og arbejdsstilling – og de fås med en række muligheder for ekstraudstyr som fx LED-lys. I forvejen leverede ExamVision mindre visirer som tilbehør, men COVID-19 medførte en meget stor efterspørgsel efter et full-face ansigtsvisir. Så da tandlægerne og kirurgerne i bl.a. Danmark genoptog arbejdet efter den første COVID-19 bølge med påbud om at bære ansigtsvisir, var det derfor et krav også at kunne tilbyde komplette ansigtsvisirer som en add-on til lupbrillerne. På den måde ville lægerne ikke skulle bære et ekstra stel, men kunne nøjes det stel der allerede var tilpasset. Men det skulle gå stærkt med at udvikle og producere det nye visir samt den nye adapter, som fastgør visiret til brillestellet. Derfor faldt valget på 3D-print, som man kunne få lavet på Teknologisk Institut.
Viden om 3D-print fra tidligere projekt med Teknologisk Institut
Kendskabet til 3D-print teknologien havde ExamVision fra et InnoBooster-projekt, som man lavede med Teknologisk Institut et år tidligere. Her fik ExamVision lavet en ny letvægts-løsning med batteripakke og lys til deres briller, da den eksisterende løsning ikke kunne holde batteri en hel dag. Denne løsning blev lavet i et samarbejde mellem afdelingerne for Industriel 3D-print og Elektriske Systemer, og resultat blev, at ExamVision fik de færdige specifikationer og den færdige elektronik til et produkt, der var klar til at CE-mærke og sætte i produktion med bl.a. sprøjtestøbning.
Lad os hjælpe dig med 3D-print produktion
Med erfaringerne fra dengang vidste ExamVision, at 3D-print er et stærkt værktøj i udviklingsfasen – især når det skal gå hurtigt – og man vidste lige præcis, hvor på Teknologisk Institut man skulle henvende sig.
Lynhurtigt udviklings- og produktionsforløb
Kort efter meldingen om, at tandlæger og kirurger i flere lande var på vej tilbage til klinikker og sygehuse efter COVID-19, kontaktede ExamVision derfor Center for industriel 3D-print med følgende melding: ”Vi har travlt – vi skal have fremstillet nogle emner.”
- ExamVisions interne designer designede hurtigt fem forskellige bud på clips til at sætte på brillerne som en click-on løsning, så man kunne montere ansigtsvisiret direkte på brillestellet med velcro i stedet for at skulle have yderligere et visirstel udenpå, fortæller Mads Østergaard, som er 3D-print ekspert og sektionsleder på Teknologisk Institut.
Designfilerne på de fem clips blev sendt til Teknologisk Institut mandag, og samme dag blev et 3D-print i nylon sat over. Tirsdag blev de printede emner sendt til ExamVision, som efter modtagelsen onsdag testede dem på deres briller for at se, hvordan clipsene passede, og om de kunne holde. Herefter blev der sendt to-tre nye designs retur til Teknologisk Institut, hvor de blev sat over til print torsdag, så de var klar fredag. Det betød, at ExamVision havde den anden designudgave i hånden mandag, hvor de endnu engang testede. Herefter blev designet rettet til en sidste og sendt til Teknologisk Institut, hvor det printet i 10 eksemplarer, som fik fjernet pulver og blev indfarvet.
Om fredagen – mindre end to uger efter at første designstreg blev trukket - da de endelige versioner var testet og godkendt, lagde ExamVision i første omgang en ordre på 4.000 stk., så der var adaptere til 2.000 briller.
De første 1.100 stk. kom med i et byg samme dag, så de var klar til afblæsning, indfarvning og forsendelse mandag eftermiddag. På den måde kunne ExamVision komme i gang med deres produktion og samleproces allerede tirsdag – fredag var yderligere 2.500 stk. produceret og afsendt, og mandag blev de sidste 4.00 stk. sendt afsted.
- Hvis alle 4.000 emner skulle printes på én gang, ville det tage ca. tre dage, men her skulle emnerne passes ind i en igangværende produktionsplan. Alligevel blev hele ordren stadig leveret inden for en uge, og i alt tog hele forløbet ikke mere end tre uger inklusive tre designiterationer, test og færdig produktion – og faktisk var forsendelserne det, der tog længst tid, da filerne kunne leveres med det samme, fortæller Mads Østergaard.
Billigere og hurtigere end sprøjtestøbning
Den store fordel ved 3D-print i forløb som dette er, at time-to-market er utrolig kort, hvilket også var påkrævet på grund af de specielle omstændigheder og den deraf følgende efterspørgsel. Normalt ville sprøjtestøbning også være oplagt til denne type emne, men i dette tilfælde ville det have taget for lang tid at lave formen, og derfor var 3D-print nødvendigt for at møde den akutte efterspørgsel. Ofte er 3D-print oplagt i netop ramp-up-fasen. Desuden skulle ExamVision ikke tænke på værktøj til fremstilling, og ved et styktal som dette var 3D-print faktisk billigere end sprøjtestøbning.
Vi var under et stort tidspres for at kunne imødekomme de mange henvendelser vi modtog på et full-face visir til direkte montering på lupbrillen. Så derfor var vi klar over, at den hurtigste og mest direkte vej til en hurtig lancering af både visir og adapter var via 3D-print. Og med erfaringerne fra det tidligere samarbejde med Teknologisk Institut, var valget af partner til denne lynopgave ret enkel. Hurtigt, effektivt og god service. Tak for det!
- Kim Jensen, CEO og chef for R&D, ExamVision
For lige at understrege, hvor hurtigt udviklingen gik, var ExamVision faktisk i gang med at reklamere for produktet på deres hjemmeside allerede efter en af de første design-iterationer – som også er den, der ses på produktbilledet.