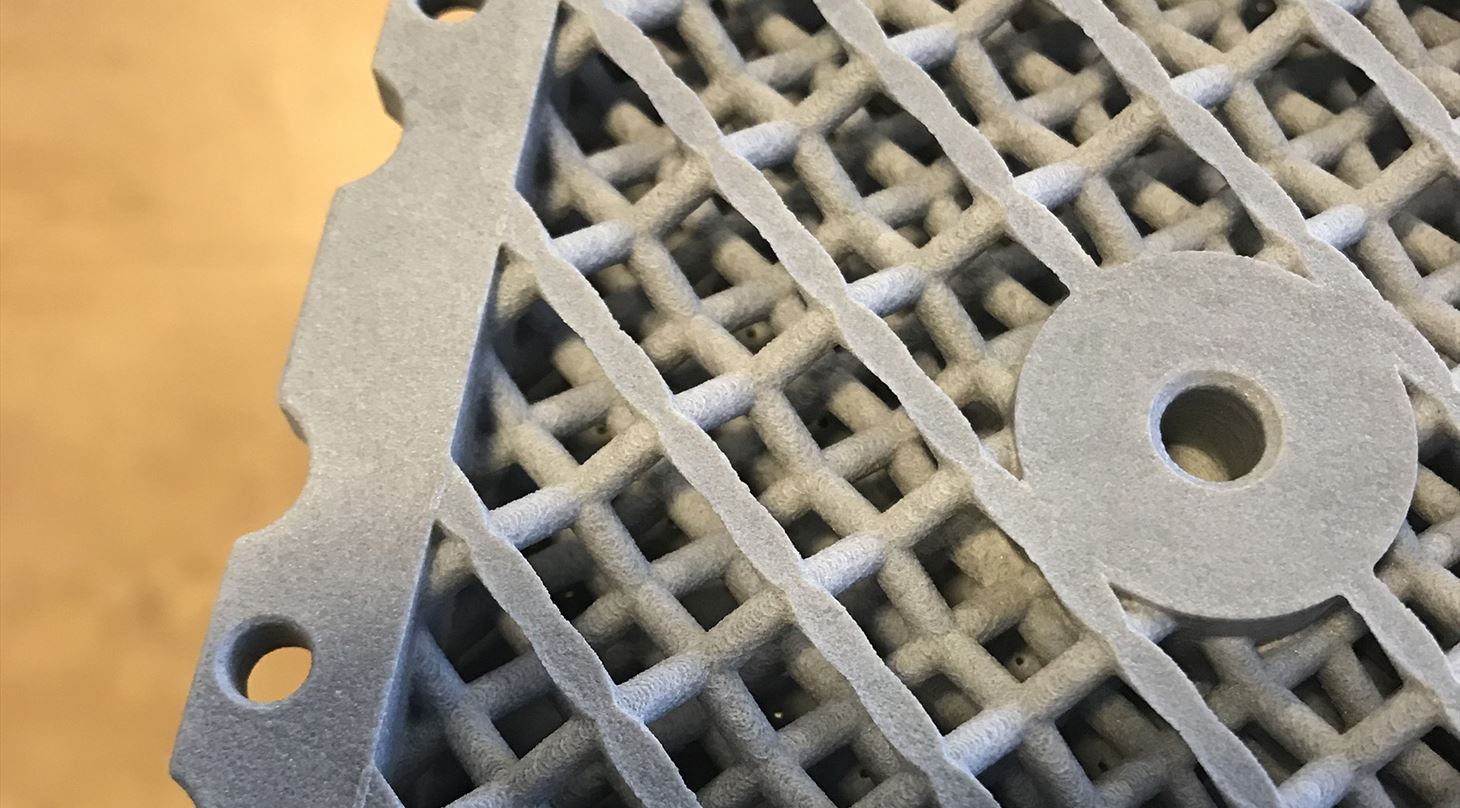
3D-printede dele til støbeprocessen gav større designfrihed og hurtig omskiftelig produktion
Virksomheden BEWI producerer til dagligt Flamingo®, hvortil der anvendes støbeværktøj lavet i aluminium til tryk på flamingo. Da BEWI deltog i et MADE demonstrationsprojekt, var det med en nysgerrighed på at undersøge, om det var muligt at implementere 3D-print til dele af deres støbeværktøjer. I samarbejde med Teknologisk Institut viste det sig, at implementeringen af 3D-print til støbeprocessen hos BEWI, var billigere at fremstille og gav kortere produktionstid. Samtidig blev det muligt at imødekomme markedets efterspørgsel på komplekse og forskelligartede geometrier takket være 3D-prints store designfrihed.
Virksomheden BEWI anvender til dagligt også støbeværktøj lavet i aluminium til at støbe emner i Flamingo® med logoer. Når et emne skal formgives, kræver det en damp og kølevands gennemgang i værkstøjsvæggen samt en høj varmeledningsevne. Problemet for BEWI opstod, da flere af deres kunder efterspurgte komplekse og forskelligartet geometrier - det stiller nemlig omfattende krav til værktøjsopbygningen, og her oplevede BEWI begrænsninger i støbeprocessen.
Lad os hjælpe dig med 3D-print produktion
”Fleksibiliteten er mere end velkommen”
Derfor blev BEWI interesserede i at undersøge mulighederne ved at anvende 3D-printede parter som en del af støbeprocessen i et forsøg på at imødekomme markedets efterspørgsel på komplekse og forskelligartede geometrier. Her gav MADE-projektet et indblik i, hvordan 3D-print kunne indfri BEWIs ønsker uden at kompromittere den konventionelle produktion. 3D-print viste sig nemlig at kunne tilgodese BEWIs ønske om kundetilpassede løsninger og en hurtig omstilling af produktionen, som er afgørende i et omskifteligt marked.
De detaljer vi laver på nuværende tidspunkt, er til tider på kanten af gravør-arbejde, og det er noget, der både koster tid og penge, hvis man skulle fræse det frem i aluminium. Nogle af de emner vi støber, skal til tider kun bruges én gang, og så skriger det jo det næsten på 3D-print, hvor fleksibiliteten er mere end velkommen
- Ole Krebs, BEWI
- De detaljer vi laver på nuværende tidspunkt, er til tider på kanten af gravør-arbejde, og det er noget, der både koster tid og penge, hvis man skulle fræse det frem i aluminium. Nogle af de emner vi støber, skal til tider kun bruges én gang, og så skriger det jo det næsten på 3D-print, hvor fleksibiliteten er mere end velkommen, lyder det fra Ole Krebs, udviklingschef hos BEWI.
Forsøget rentabilitet og forkortet produktionstid
At 3D-print var et oplagt valgt for BEWIs omskiftelige produktion, var blandt andet muligheden for at forkorte produktionstiden, fordi man netop ved 3D-print slipper for at skulle fræse emnet, hvilket er rentabelt på arbejdstimer og produktionstiden.
- 3D-print har givet nogle andre muligheder, end når vi får lavet et konventionelt værktøj. Ved 3D-print laver du i stedet en fil, som du efterfølgende kan trykke print ved. Det er altså ikke det samme som at skulle sidde og fræse fysisk i en aluminiumsklods, fortæller Steen Storgaard, designer hos BEWI.
MADE Demonstrationsprojektet har givet en unik sparring
For BEWI har deltagelsen i MADE Demonstrationsprojektet været et nyt tiltag, der har givet en unik sparring til at undersøge mulighederne inden for 3D-print.
- Det har været nyt for os at skulle række ud, fordi vi typisk har søgt inspiration inden for vores egen branche eller noget, der er beslægtet med det, vi selv kommer fra. Ved at skulle række ud til et institut som Teknologisk Institut har vi skulle forklare, hvad det er, vi går og laver i vores dagligdag. Det har været en vigtig læring, fortæller Ole Krebs.
Artikel er oprindelig publiceret i anden form af MADE
MADE Demonstrationsprojektet er muliggjort ved finansiering fra Industriens Fond.