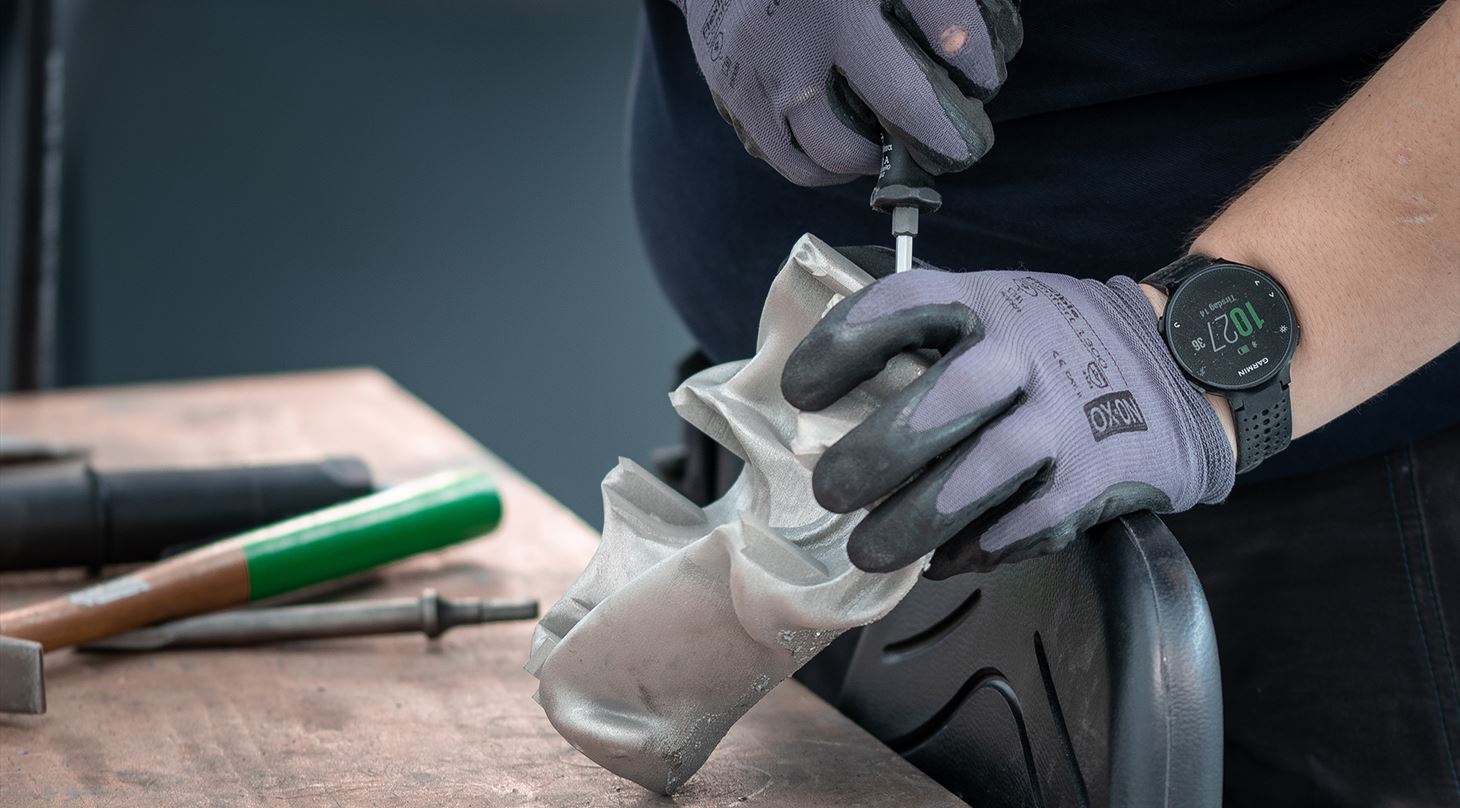
3D-printede redskaber sætter Danfoss i nyt gear - De er lettere, stærkere og billigere at producere
Danfoss har i AM-LINE 4.0-projektet udviklet 3D-printede værktøjer, der er stærke, men samtidig så lette, at de mange løft for operatører på fabriksgulvet er nemmere. Med 3D-print teknologien har vi lært at kravle, nu er tempoet i gågear – og i fremtiden vil vi løbe, lyder det fra Danfoss Heatings leder af AM. Resultaterne er unikke, vurderer Teknologisk Institut.
Lighter, better, faster, stronger.
Daft Punks ikoniske sang kan med en lille omskrivning fungere som soundtrack til Danfoss’ udvikling inden for 3D-print, der er en vigtig del af digitaliseringsstrategien i Danmarks største industrivirksomhed.
I AM-LINE 4.0-projektet har den danske industrigigant bl.a. skabt to nye applikationer: 3D-printede redskaber, der er lettere, stærkere, hurtigere og samtidig billigere at producere – mens komponenternes levetid er fem gange længere sammenlignet med konventionel fremstilling. Der er tale om et redskab til montering af elektriske motorer og et 3D-printet armatur i titanium.
- Det motiverede os at udvikle lettere redskaber, der minimerer operatørernes daglige belastning og dermed minimere risikoen for skader. Samtidig er det en gevinst, at 3D-printet metal i lav volumen er konkurrencedygtig på prisen, siger Niklas Franke, Head of Additive Design and Manufacturing hos Danfoss Heating.
Innovationen er sket i tæt samarbejde med Teknologisk Institut, der i AM-LINE vejleder og producerer for både små og store virksomheder, så de kan komme i gang med 3D-print.
- Danfoss er blevet mere åbne over for, at 3D-print ofte kan være en rigtig god mulighed. Danfoss har flere og flere efterspørgsler, og de har fået øjnene op for, hvor mange forskellige steder, de kan bruge teknologien. Det tror jeg ikke, de var klar over før, vurderer Anders Bæk Hjermitslev, konsulent ved Industriel Materialeteknologi hos Teknologisk Institut.
Og udviklingen er ikke kun sød musik i ørene for Danfoss, for målet med AM-LINE 4.0 er nemlig at dele viden med andre produktionsvirksomheder, så metal 3D-print bliver udbredt i Danmark til gavn for alle.
De pulserende toner rammer også meget godt udviklingens upbeat tempo: 3D-print vokser med raketfart.
Make it better, Do it faster: Nyt værktøjer letter byrden
Værktøjet til montering af den elektriske motor i Danfoss’ kompressorer – et stator centreringsredskab – er cirka lige så stor som en halv liter vandflaske.
Det afgørende her var at fjerne al unødvendigt materiale for at reducere vægt og pris, men samtidig beholde nok masse til, at værktøjet var tilpas robust, fortæller Niklas Franke. Med nye materialer og en unik gitterstruktur er værktøjets vægt formindsket med hele to tredjedele – fra 1.100 g. til 382 g.
Før anvendte vi f.eks. en særlig slags aluminium, og så skiftede vi til 3D-printet titanium, der er meget stærkere. Med traditionelle fremstillingsmetoder er det ikke muligt at skabe den komplekse geometri, der er afgørende for vægtreducering
- Niklas Franke, Danfoss
- En vægtreducering på to tredjedele har en stor betydning for operatørerne, når de skal løfte 180 gange om dagen. Samtidig bliver værktøjet også stærkere og bedre. Det er en ret unik løsning, der er ikke mange andre virksomheder, der har sådan et værktøj, vurderer Anders Bæk Hjermitslev fra Teknologisk Institut, der har været med til at bearbejde 3D-print ideerne fra Danfoss og løbende haft dialog med Niklas Franke om, hvilke designs der fungerer bedst ud fra Danfoss’ ønsker.
3D-printet armatur i titanium
Den anden applikation er et armatur, der tester Danfoss-ventiler i laboratoriet ved at sætte dem under pres (op til 200 bar). Førhen blev der anvendt stål, men den nye applikation består af 3D-printet titanium, der er hele 77 procent lettere.
- Ved hjælp af simuleringer vejer redskabet nu 2,8 kg. frem for 12 kg., og et lettere armatur gør det nemmere at teste forskellige procedurer af, fortæller Niklas Franke.
Prisen har også fået et nyk nedad: Fra 50.000 kr. til 32.500 kr.
- Selv om tilgangen med at designe emner ud fra simuleringer er spæd, så kan løsningen allerede nu anvendes til at skabe resultater – også for folk, der ikke er eksperter i simuleringer, vurderer Niklas Franke.
Hvorfor er 3D-print ideelt til at skabe lette, stærke produkter?
- Der kan fremstilles helt unikke geometrier. Materialeegenskaberne ved 3D-print er bedre end mange andre fremstillingsmetoder – på grund af den mikrostruktur, der bliver opbygget i materialet, men også de materialer, man kan bruge til 3D-print, siger Anders Bæk Hjermitslev.
Hvad kan andre virksomheder lære?
Danfoss har ifølge deres samarbejdspartner grund til at være glade for de to nye redskaber:
- Det er en super god case, som mange små virksomheder kan spejle sig i og se, at de nok også har nogle lignende værktøjer, som kan forbedres, vurderer Anders Bæk Hjermitslev fra Teknologisk Institut, der i november 2020 delte ud af sin viden om 3D-printet metal ved MADE AM-LINE Open Lab ’Helt klar til fabriksgulvet’.
Virksomheden selv mener også, der er viden at hente for andre.
- Alle produktionsvirksomheder skal håndtere forsyningskæder, hvor forskellige typer af værktøj er anvendt. De fleste redskaber anvendes i lav-volumen, og det gør dem ideelle for 3D-print – ligegyldigt, om der er tale om metal eller plastik, forklarer Danfoss Heatings AM-leder.
Fra gå til løb
I AM-LINE har Danfoss fået ny indsigt i, hvordan teknologien kan kobles på applikationer på fabriksgulvet.
- Vi har opnået det, vi gerne ville. Før vi løber, skal vi lære at gå. I de sidste tre år har vi lært i AM-LINE, hvordan vi bevæger os i gåtempo med 3D-print, forklarer Niklas Franke, der er glad for, at Danfoss med de to nye redskaber er på forkant med teknologien, men erkender også, at det er en ´dråbe i havet´.
- Vi vil anvende erfaringen fra MADE og AM-LINE 4.0 til at opskalere vores succeser. Vi har udviklet fire-fem nye værktøjer, men i Danfoss har vi tusinder af lignende redskaber, som vi gerne vil gøre så lette som muligt, da de bliver båret fra a til b i fabrikken. Vi skal opskalere, så vi er i stand til at løbe.
Deres sparringspartner stemmer i:
- Det er jeg enig i. Danfoss’ primære fokus har været at sprede kendskabet til teknologien rundt i deres store organisation, og nu er de så ved at finde de gode business cases, siger Anders Bæk Hjermitslev.
Muligheden for at skrue tempoet i vejret er lige rundt om hjørnet:
- Fremskridt inden for simuleringsevner vil gøre det nemmere og hurtigere at udvikle den ideelle løsning på et problem. De optimale løsninger vil være langt mere komplekse og organiske i forhold til det, vi ser i dag. 3D-print er en perfekt fremstillingsmetode, når det kommer til at realisere fremtidens løsninger, og bedre simuleringer vil skubbe yderligere til adopteringen af 3D-print i fremstillingsindustrien, siger han.
Digitale tvillinger kan for Danfoss blive relevante på den lange bane.
- Digitale tvillinger er at løbe, men vi er fortsat fokuserede på at gå, siger Niklas Franke.
Den disposition giver god mening, hvis man spørger eksperten tilknyttet Center for Industriel 3D-print i Aarhus:
Danfoss har taget de første skridt. De har allerede en del gode cases, og jeg er ikke i tvivl om, at inden for et år eller to, så begynder det virkelig at tage fart. Når de her cases er blevet implementeret, så vil det gå virkelig stærkt
- Anders Bæk Hjermitslev, Teknologisk Institut