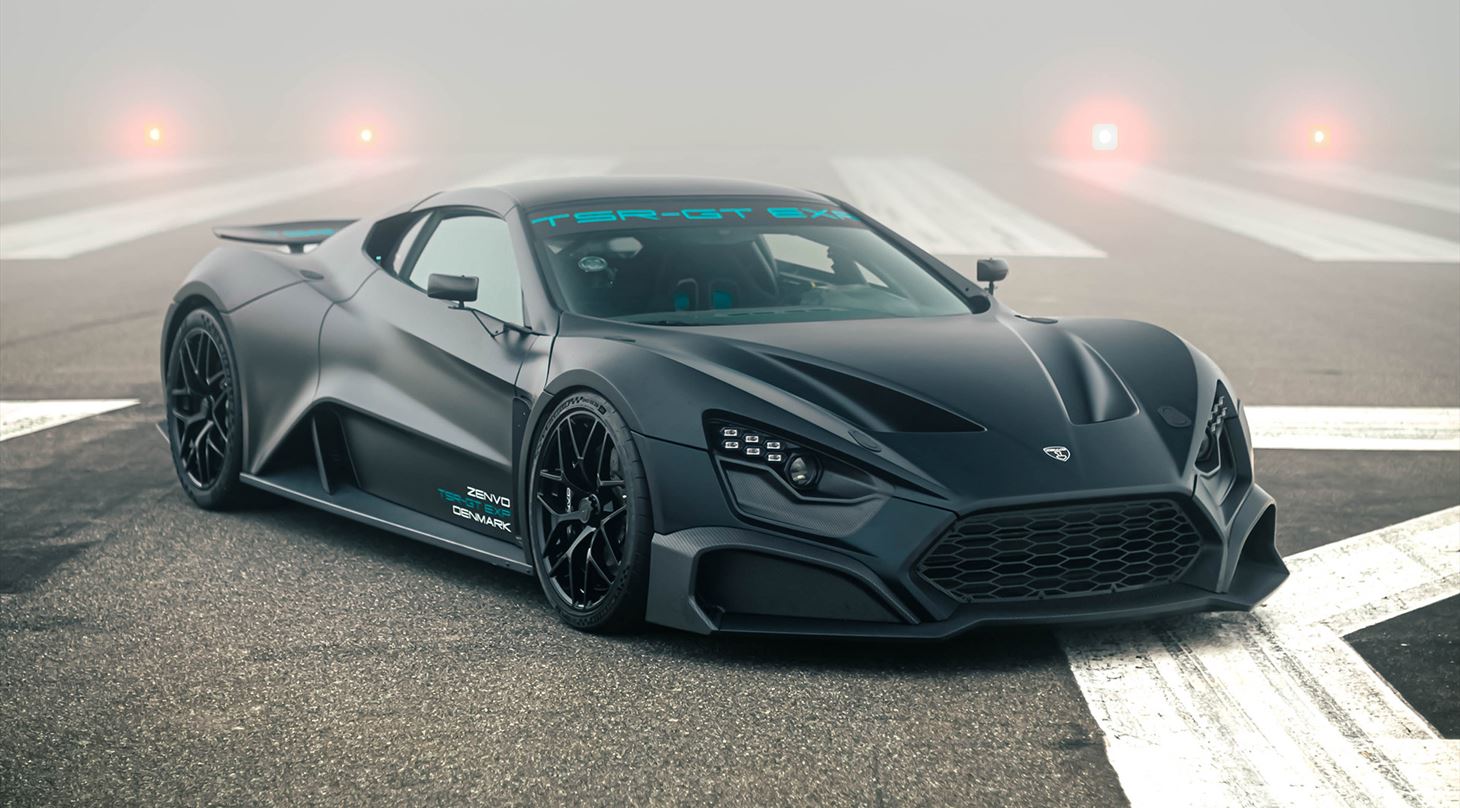
Hjulophæng til Zenvos hyperbil blev designoptimeret til 3D-print
Zenvo er en dansk sportsvognsfabrikant, der håndbygger såkaldte hyperbiler på deres fabrik i Præstø. Virksomheden har benyttet 3D-print i plast til tidligere bilmodeller, og derfor valgte man at undersøge, om metal 3D-print kunne hjælpe med at optimere et hjulophæng.
Zenvo bygger eksklusive køretøjer i ultra-lav volumen, og man har således ikke brug for enorme styktal af de enkelte komponenter – til gengæld har man brug for komponenter, der både er lette, optimerede og visuelt fængende, og her var det nærliggende at ty til metal 3D-print.
Hos Zenvo valgte man derfor at deltage i designoptimeringsforløbet DfAM Green (Design for Additive Manufacturing), som er initieret af Dansk AM Hub. I forløbet, der ligeledes har som mål at øge bæredygtigheden for de komponenter, der arbejdes med, fokuserede man sammen med 3D-print specialisterne fra Teknologisk Institut på at optimere et hjulophæng.
I forløbet har Zenvos oprindelige design gennemgået en række ændringer, der har haft som mål at reducere vægten og generelt optimere hjulophænget. Tidligere bestod hjulophænget fx af seks komponenter, men i det nye design er de samlet til én enkelt komponent. Under DfAM Green-forløbet er produktionen af hjulophænget desuden blevet flyttet fra Kina til Danmark for at skære den CO2-tunge transport ud af regnestykket.
På en enkelt del sparer vi et halvt kilo, så hvis du ganger det med fire, fordi du har fire hjul på bilen, så er det to kilo per bil. Det gør en stor forskel i vores verden
- Alberto Solera, Zenvo Automotive A/S
I designprocessen har man brugt såkaldt topologioptimering, hvor komponenten gennemgår en række computerberegninger og -simuleringer. Det betyder, at man kun ender med den nødvendige mængde materiale til at skabe den nødvendige styrke, der hvor den er påkrævet. Samtidig betyder det, at man ender med en unikke organiske former, som det ses på billedet herover.
- Det nuværende hjulophæng var ret klodset og tungt, og i hyperbil-verdenen skal komponenter også være behagelige for øjet. Resultaterne af det 3D-printede hjulophæng er en ydeevne-gevinst, da det er lettere og stærkere. Det er lidt dyrere, men fordi det er mere æstetisk behageligt for øjet, er det en omkostning, vi er villige til at betale, fortæller Alberto Solera, Technical Director – TS Series hos Zenvo Automotive.
I videoen herunder kan du høre om forløbet med at designoptimere hjulophænget.
Lavere vægt og mindre materialeforbrug
Den nye komponent er blevet printet i aluminiumslegeringen AlSi10Mg med 3D-print teknologien Laser Powder Bed Fusion. Ved hjælp af topologioptimering er hjulophængets vægt reduceret med 28 procent - fra 2,621 kg til 1,883 kg - og dets volumen er ligeledes blevet reduceret med 25 procent, fra 933 cm3 til 700 cm3. Desuden har vægtreduceringen og optimeringen i produktionsprocessen resulteret i en besparelse på hvad der svarer til 2,6 ton C02.
- Ved at designe komponenter, som er topologioptimeret, anvendes der mindre materiale i produktionsprocessen. Som resultat af materialereduktionen nedbringes CO2-udledningen. Hjulophænget ender derfor med at være bedre for klimaet - både i kraft af den reducerede mængde materiale og det lavere energiforbrug i selve produktionsprocessen, fortæller Sigurd Vigen, konsulent hos Teknologisk Institut.
Bedre rustet til fremtiden med 3D-print
Zenvo har i løbet af DfAM Green-forløbet fået øjnene op for potentialerne ved metal 3D-print. Man er blevet klogere på, hvornår det giver mening at topologioptimere og 3D-printe og er således langt bedre rustet til næste gang, man skal have indkørt en komponent til 3D-print.
Det 3D-printede hjulophæng er testet succesfuldt på fabrikken, og næste skridt efter projektet er test på vejene.
- Vi tager hjulophænget og monterer det på en bil og laver nogle test i den virkelige verden. Og hvis alt går godt, hvilket jeg er meget sikker på, at det vil, kommer det i produktion, lyder det afsluttende fra Alberto Solera.
Om DfAM Green
I løbet af det seneste halve år har Dansk AM Hub i samarbejde med partnerne Teknologisk Institut, Hexagon og Implement Consulting Group haft fire danske SMV’er tilknyttet et innovationsforløb med henblik på at styrke virksomhederne til i endnu højere grad at drage fordel af det bæredygtige, teknologiske, bærdygtige og forretningsmæssige potentiale inden for 3D-print. Forløbet har fået navnet Design for Additive Manufacturing Green (eller DfAM Green) og fokuserer på at udbrede 3D-print til små- og mellemstore virksomheder samt at yde konkret støtte og hjælp til at arbejde med teknologien igennem design. Det konkrete mål for DfAM-forløbet er at re-designe deltagernes produkter eller komponenter, så de bliver mere bæredygtige og samtidig kan fremstilles med fx større styrke, mindre materialespild, ny og bedre funktionalitet eller on-demand.