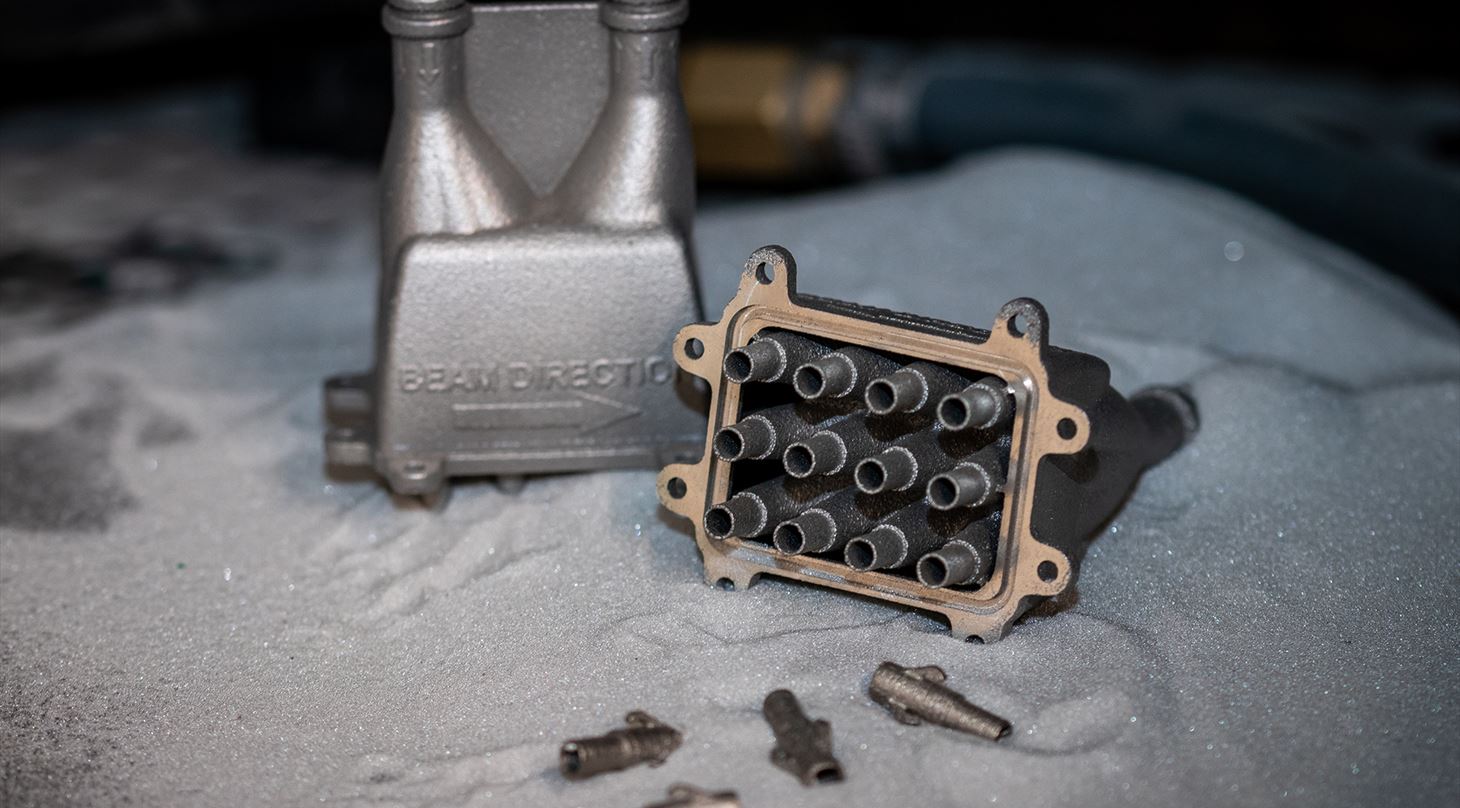
Kompakt køleelement blev 3D-printet i aluminium
Da JJ X-Ray skulle udvikle et nyt køleelement til et af deres instrumenter, var der behov for en meget kompakt løsning med uhindret flow af vand. På grund af designfriheden og en attraktiv pris ved lave styktal var 3D-print i aluminium den helt rigtige løsning, og emnerne – som blev printet på Teknologisk Institut – fungerede perfekt.
JJ X-Ray er en mindre dansk virksomhed, som designer og fremstiller high-end løsninger til høj-præcisions instrumenter, hvor stor holdbarhed ligeledes er vigtigt. Det kunne fx være udstyr til videnskabelige eksperimenter, hvor målgrupperne er forskningsmiljøerne inden for analytisk røntgen- og synkrotronstråling.
Disse løsninger er tit meget avancerede, og der er høje krav til de forskellige komponenter – fx i forhold til vakuum-tæthed, overflader og tolerancer. Det var også tilfældet, da JJ X-Ray skulle udvikle en ny køler til et instrument. Instrumentet skulle bruges til køling af en såkaldt White Beam Slit hos Catereté Beamlinet ved det brasilianske LNLS laboratorium (Brazilian Synchrotron Light Laboratory), hvor den afsatte effekt fra en røntgenstråle er op til 1500W.
Behov for specielle egenskaber
Køleren skulle udvikles helt fra bunden, og den skulle være meget kompakt for at passe ind i instrumentet, samtidig med at der skulle være vand-flow med meget lidt modstand – derfor skulle den naturligvis også være helt tæt. Denne kombination betød, at der skulle en kompleks geometri til, og derudover skulle der også indbygges vibrationsdæmpning i dyse-enderne.
Der skulle kun produceres få styk af kølerne, og der var i øvrigt fokus på at holde prisen nede. Derfor begyndte designerne hos JJ X-Ray at kigge på 3D-print.
3D-print var den (eneste) rigtige løsning
JJ X-Ray kontaktede Center for Industriel 3D-print på Teknologisk Institut, som tilbyder 3D-print i metal. Her fik man rådgivning om de forskellige muligheder, og Teknologisk Institut hjalp med at optimere det design, som JJ X-Rays udviklingsafdeling havde lavet, så det kunne printes til den lavest mulige pris.
Valget faldt på 3D-printet aluminium, som er relativt billigt i fht. rustfrit stål og titanium, da man kan printe virkelig hurtigt, fordi aluminium hurtigt optager varmen fra laserne. De små fjedre er printet i rustfri stål 316L for at holde styrken og elasticiteten høj. Baggrunden var som sagt et ønske om et kompakt emne med mindst mulig flow-modstand, og med 3D-print endte man med en simpel løsning, som var let at installere, fordi elementerne kunne samles i én komponent. Skulle køleren være lavet med traditionelle metoder, ville der være mange forskellige samlingspunkter.
- Inde i køleren kører indgangs- og udgangsflowet meget tæt op og ned ad hinanden i indvendige kanaler, der folder sig ind i hinanden – en såkaldt manifold. Denne løsning kan kun laves med 3D-print, og den er med til at gøre køleren ekstra kompakt, fortæller Lasse Haahr-Lillevang, som er 3D-print ekspert på Teknologisk Institut og har arbejdet med løsningen til JJ X-Ray.
Kølerne blev printet på Teknologisk Instituts metalprintere, og her sørgede man også for, at emnerne fik den helt rigtige efterbehandling for at opnå de ønskede overfladeegenskaber.
Hele komponenten består af tre forskellige dele – hhv. kølehoved, dyse-hoveder og et rør imellem. De første to er printede, mens røret blev købt for at holde prisen nede, men det hele kunne også være 3D-printet i ét stykke.
Billigere end alternativerne
3D-print var en billigere løsning end traditionel fremstilling, fordi styktallet var meget lavt (4 sæt i alt - 4 x kølehoveder i aluminium og 4 x 12 fjedre i rustfri stål 316L). Men lige præcis denne løsning ville heller ikke give mening - eller være mulig - at lave på anden vis, fordi den er så kompakt og kompleks - så skulle den designes helt anderledes. Dermed gav 3D-print det absolut bedste fit mellem høj performance og lav pris, og business casen ville stadig være god, hvis der skulle produceres 1.000 stk. af køleren. Hos JJ X-RAY er man også meget tilfredse med løsningen.
Med 3D-print fik vi mulighed for at optimere vandflow og styrke i et meget kompakt design, og det var ikke muligt med en svejset konstruktion. Derfor var 3D-print den helt rigtige løsning for os.
- Jacob Navntoft, JJ X-Ray
De 3D-printede kølere er i dag i brug sammen med instrumentet, og de yder, som de skal. Dog erfarede JJ X-Ray i montageprocessen, at aluminium var lidt blødt til formålet, så det var svært at pakke mod flangen – men det lykkedes. Dog vil man næste gang vælge rustfrit stål 316L eller titanium til formålet.
Desuden betød forløbet, at JJ X-Ray og ikke mindst virksomhedens designere fik værdifuld erfaring med 3D-print, som de kan bruge til fremtidige løsninger, som skal være skræddersyede og i små styktal.