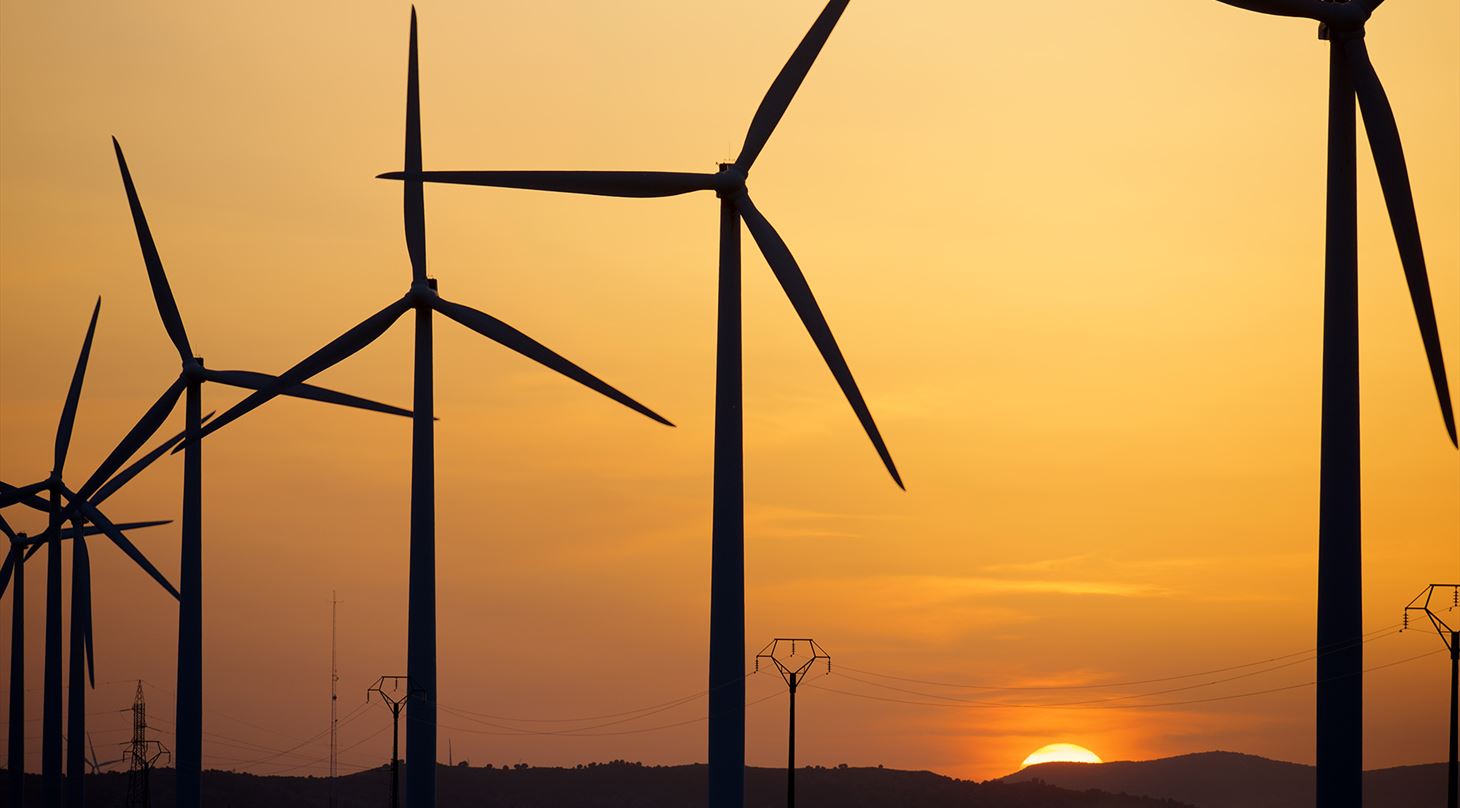
Med 3D-print er der medvind på materialespild og klimaaftryk
Case lavet i foråret 2022
KK Wind Solutions fik under et 3D-print designforløb mulighed for at optimere en af deres kobber-komponenter – og resultatet gav medvind med både forøgelse af komponentens funktioner samt en reduktion af materialeforbruget.
Som navnet antyder, beskæftiger KK Wind Solutions sig til dagligt med vindmølleindustrien, hvor man tilbyder automatiseringsløsninger til moderne vindmøller samt systemløsninger inden for grønne energikilder. Forud for deltagelsen i 3D-print designforløbet DfAM – Design for Additive Manufacturing -som er initieret af Dansk AM Hub, havde KK Wind Solutions sat sig ved tegnebrættet for at udvikle nye komponenter med mindre materialespild. Derfor var timingen for DfAM oplagt, og KK Wind Solutions sagde uden tøven ja til at deltage i forløbet, hvor de bl.a. samarbejdede med Teknologisk Institut.
- Målet med optimeringen var både at bruge mindre materiale samt opnå en bedre køling – altså simpelthen at udnytte materialet bedre. Hvis man skulle i gang med at fræse eller dreje komponenten, ville man skulle starte med en stor klump kobber, som skulle fræses til, og der ville opstå et stort spild. Så ved at anvende 3D-print i forløbet, har vi fået mulighed for at reducere spildet, og det har været meget fordelagtig, lyder det fra Poul Seerup Thing, Lead Engineer hos KK Wind Solutions.
Målet har været at reducere materialespild
Komponenten, der skulle optimeres med metal 3D-print, var en såkaldt kobber-busbar. Den kan bl.a. sidde i en vindmølles konverter, der konverterer vindenergi til strøm, og samtidig kan den fx erstatte en kobberskinne eller en ledning.
- Vi havde været i gang med at designe nogle emner i kobber, hvilket passede godt med, at vi i forløbet kunne få printet emnerne en-til-en med virkeligheden, da vi førhen har printet prototyper med vores plastfilament-printer, siger Jørgen Dahl Vestergaard, Director Specialist hos KK Wind Solutions og tilføjer:
Så vi stod i en situation, hvor vi skulle finde ud af, om vi skulle printe emnerne i kobber eller aluminium, hvilket spillede ret godt sammen med, at vi fik muligheden for at koble os op på DfAM-forløbet
- Jørgen Dahl Vestergaard, KK Wind Solutions
Fik mulighed for at gøre komponenten mere attraktiv
KK Wind Solutions fremhæver også, hvordan det positive resultat omkring reducering af materialespild kan have en positiv betydning for klimaaftrykket i udarbejdelsen af komponenten:
- Kobber er et dyrt materiale, som skal graves op af jorden. Så i stedet for at sætte et stort klimaaftryk ved at bruge kobber, kunne vi undersøge et andet materiale og anden produktionsmetode. Derved kunne vi gøre komponenten mere attraktiv både kostmæssigt og anvendelsesmæssigt samt koble flere funktioner sammen. Det er noget af det, vi har fokuseret på undervejs, og der må man sige, at 3D-print hurtigt bliver mere interessant end andre produktionsmetoder, siger Jørgen Dahl Vestergaard.
I stedet for kobber, som ellers har en god varmeledningsevne, blev busbaren 3D-printet i aluminium, som er billigere. Men ved at designe den med gitterstrukturer, som øger overfladearealet, forventes aluminiumsudgaven at have en ledningsevne på niveau med kobber på grund af en forbedret afkøling.
”Det er en ny måde at tænke design på”
Selvom KK Wind Solutions allerede havde givet sig i kast med 3D-print i plastik, var der store opdagelser og ny viden at finde ved at prøve Teknologisk Instituts metal 3D-printere til print af busbaren.
- Man kan tale for designfriheden ved 3D-print og det, at man kan lave nogle geometrier, som ikke kan produceres på anden vis. Det giver faktisk et helt andet løsningsrum, og hvis man samler flere forskellige funktioner i det samme emne, kan man integrere på uendeligt mange måder, samtidig med at man for eksempel også har en god serviceadgang og køling. Det er en ny måde at tænke design på, lyder det fra Jørgen Dahl Vestergaard.
DfAM-forløbet har givet et større netværk og konkrete designforslag
Ved spørgsmålet om, hvilken gevinst der har været ved at deltage i DfAM-forløbet, fremhæver Jørgen Dahl Vestergaard og Poul Seerup Thing, hvordan forløbet både har givet et større netværk og kendskab til markedet inden for 3D-print.
- Derudover har vi fået et helt konkret designforslag til et helt konkret emne, som vi får testet og vurderet i forhold til et klassisk design. Kommer det til at gå godt, kan vi kvalificere vores tanker og ideer i forhold til materialebesparelser og lave en komponent med flere funktioner, fortæller Jørgen Dahl Vestergaard.
Ydermere påpeger Poul Seerup Thing, hvordan alle virksomheder, kan få gavn af det tværfaglige samarbejde i DfAM-forløbet:
Det kan være en øjenåbner for alle mulige virksomheder, uagtet hvilket niveau man befinder sig på. Så selvom man ikke har noget kendskab til 3D-print, så giver det bare nogle nye muligheder at se, hvad fx de nye plastik 3D-printere også kan, hvilket jeg bestemt synes er værd at tage med
- Poul Seerup Thing, KK Wind Solutions
Fakta om løsningen:
- Materiale og teknologi: Aluminium printet med Laser Powder Bed Fusion
- Vægtreduktion: Part 1 = 96% - Part 2 = 91%
- Forøgelse af overfladen: Part 1 =129% - Part 2 = 162%
Kort om DfAM-forløbet
I løbet af det seneste halve år har Dansk AM Hub i samarbejde med partnerne Teknologisk Institut, PLM Group, Hexagon og Wikifactory haft 15 danske SMV’er tilknyttet et nyt innovationsforløb med henblik på at styrke virksomhederne til i endnu højere grad at drage fordel af det teknologiske og forretningsmæssige potentiale inden for 3D-print. Forløbet har fået navnet Design for Additive Manufacturing (eller DfAM) og fokuserer på at udbrede 3D-print til små- og mellemstore virksomheder samt at yde konkret støtte og hjælp til at arbejde med teknologien igennem design. Det konkrete mål for DfAM-projektet er at re-designe deltagernes produkter eller komponenter, hvilket muliggør at disse fx kan fremstilles med større styrke, mindre materialespild, ny eller bedre funktionalitet eller on-demand.