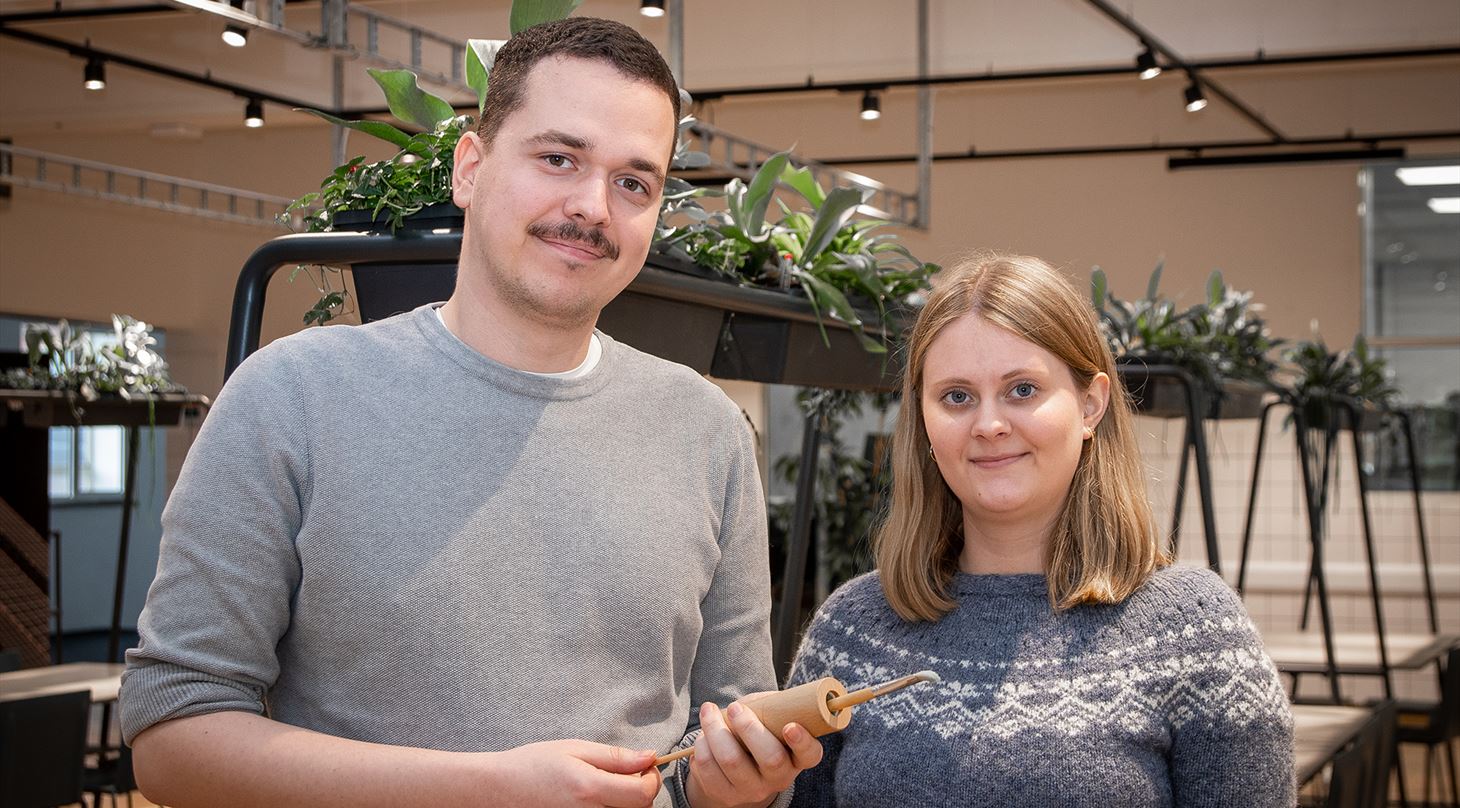
Nyt hjælpeværktøj til gigtpatienter blev udviklet med 3D-print
I samarbejde med Teknologisk Institut udviklede virksomheden Manigrip i 2019 et hjælpeværktøj til gigtpatienter, der oplever udfordringer ved at holde om smalle genstande, som eksempelvis blyanter, bestik og tandbørster. Takket være 3D-print varede hele udviklingsforløbet mindre end et halvt år, og undervejs har Manigrip haft adgang til alle kompetencer under ét tag på Teknologisk Institut.
Manigrip blev etableret i 2017 af fire iværksættere, heriblandt Henrikke Kylén Pedersen og Thomas Solgaard, men faktisk opstod ideen til hjælpeværktøjet allerede i 2016 i forbindelse med et eksamensprojekt i faget Interaktionsdesign på Aarhus Universitet. Hjælpeværktøjet er en grebsforstørrer, som kan sættes på smalle genstande og dermed give en forstørret gribeflade, og i løbet af det videre uddannelsesforløb udviklede ideen sig. Efter selv at have fået lavet de første prototyper i 2018, valgte Manigrip i foråret 2019 at kontakte Teknologisk Institut med henblik på at få færdigudviklet grebsforstørreren.
På dette tidspunkt var der stadig tale om en koncept-idé, for selvom Manigrip havde nogle simple prototyper med plasticrør og en hjemmeside omkring konceptet, var det stadig på skitseniveau. Manigrip havde selv styr på forretningsdelen af konceptet, men de manglede den tekniske baggrund og konstruktionserfaringen til at kunne realisere det, og derfor havde de behov for Teknologisk Instituts udviklingsviden til at komme videre.
Vi havde mistet en samarbejdspartner og var i en situation, hvor vi ret hurtigt skulle have en masse prototyper ud til forskellige brugere, og det eneste sted, hvor vi rigtig følte os forstået i forhold til, hvor vi var henne i processen, var på Teknologisk Institut
- Thomas Solgaard, Manigrip
I videoen herunder fortæller Manigrip om udviklingsforløbet og samarbejdet med Teknologisk Institut - casen fortsætter efter videoen.
InnoBooster satte gang i udviklingen
Efter indledningsvist at have drøftet de forskellige muligheder hjalp Teknologisk Institut Manigrip med at søge en InnoBooster på omkring 450.000 kr. som kunne bruges til at købe kommercielle ydelser i såvel Center for Industriel 3D-print som på resten af Teknologisk Institut - herunder produktudviklingstimer og 3D-printede prototyper. Det viste sig nemlig hurtigt, at de eksisterende prototyper ikke lignede det, som det færdige produkt skulle blive til.
- Da InnoBoosteren var på plads, lavede vi en plan om at køre kortere udviklingsloops på omkring 10.000 kr., så vi ikke risikerede at komme for langt ud ad en forkert tangent. Disse loops indeholdt konstruktionstimer, print, samling og test. Mellem disse loops afholdt vi statusmøder med nyudviklede prototyper lavet ved hjælp af bl.a. SLA og SLS-teknologi. Så kiggede vi sammen på prototyperne og vurderede, hvad de kunne, og hvordan de virkede, fortæller Thomas Westersø, konsulent på Teknologisk Institut og 3D-print ekspert.
Et udvilingsloop tog 1-2 uger, og på baggrund af statusmødet kom der en række tilbagemeldinger – fx at grebsforstørreren skulle være stærkere og mere stabil, at den skulle holde emnerne på en anden måde, at elektronikken skulle være på indersiden, og at den skulle kunne køre i længere tid. Hen ad vejen kom prototyperne desuden i forbrugertest, hvor gigtpatienter gav deres feedback til konceptet. De første tre loops gik således med at finde frem til en funktionel prototype, og de næste to loops blev brugt på at lave fem prototyper til forbrugertest. Efter feedback fra testen blev der lavet nogle ændringer, og efter yderligere tre-fire loops står Manigrip nu med et produktkoncept, som er klar til den endelige produktionsmodning hos producenten.
- Den store fordel ved 3D-print er, at du hurtigt får en prototype klar, og det har været ret vigtigt for vores måde at udvikle på. Vi har fra start inddraget brugere i vores udvikling, og der har 3D-print været uundværlig i den proces, fordi vi hurtigt kunne få nye iterationer på baggrund af de indsigter, vi fik tilbage fra brugerne, fortæller Thomas Solgaard, som er medstifter af Manigrip.
Undervejs i udviklingsprocessen har Manigrip haft adgang til alle nødvendige kompetencer under ét tag på Teknologisk Institut, herunder produktudvikling, 3D-print, elektronikudvikling, mekanisk sikkerhed og batterisikkerhed – det har været en stor fordel, da det har gjort det lettere at bevare overblikket og koordinere fremdriften i udviklingen.
Mangel på plads var den største udfordring
Helt konkret fungerer grebsforstørreren ved, at grebet ’lukker’ sig om forskellige aflange, tynde emner, så gigtpatienter får noget mere at holde ved end fx en tynd pensel, en kuglepen eller bestik.
Først skulle konceptet dog udvikles helt fra bunden, herunder elektronik, mekanik og hvordan det hele skulle fungere, og det eneste Teknologisk Instituts eksperter havde at gå ud fra, var nogle ydre rammer samt nogle eksempler på emner, som håndtaget skulle kunne gribe om. I en sådan proces er 3D-print et helt oplagt værktøj, fordi der er kort tid fra idé til funktionel prototype, så processen speedes op, og der kan laves flere forskellige funktionelle prototyper.
I udviklingsprocessen var en af de store udfordringer, at håndtaget skulle være forholdsvis lille, mens hullet i det skulle være forholdsvis stort. Det betød, at der var meget lidt plads til at lave mekanik, lukkemekanisme, elektronik, batteri og knap.
Efter en del idé-generering, hvor vi undersøgte og testede metoder til at lukke omkring ting på, nåede vi frem til et brugbart koncept, som vi testede i en tidlig prototype. Da vi så, at det virkede, gik vi videre med det.
- Sigurd Vigen Pedersen, Teknologisk Institut
Samtidig var det spændende at være så begrænset på plads og finde en løsning til det – hvor der samtidig er plads til både mekanik og elektronik.
Fokus på elektronikken
Da mekanikken og funktionaliteten af grebsforstørreren var på plads, var det tid til at udvikle styringen, og her kom Teknologisk Instituts afdeling for Elektriske Systemer på opgaven. De har udviklet henholdsvis software og elektronik, og det hele er specificeret, så Manigrip er godt klædt på til den endelige produktmodning.
- Vi har designet alle komponenter med henblik på at opnå mindst mulig størrelse og lavest muligt strømforbrug, og printkortet måler fx blot 2½ x 1 cm. Styringen er samtidig lavet, så vi minimerer driftstiden for motoren, og strømforbruget, når hjælpeværktøjet ikke bruges, er ligeledes minimeret. Dette sikrer brugeren lang tid mellem hver opladning, fortæller Jonas Nyborg, seniorkonsulent og elektronikekspert på Teknologisk Institut.
Han forklarer videre, at batterisikkerhed også har været et vigtigt emne. Derfor overvåges de mest kritiske batteriparametre både i softwaren og af en beskyttelsesfunktion i hardwaren. Således er alle brugs- og sikkerhedsaspekter tænkt ind i elektronikudviklingen.
Klar til produktion
For Manigrip har det fra starten været vigtigt, at grebsforstørreren blev udviklet, så den kunne produceres med sprøjtestøbning, selvom 3D-print også kunne være en mulighed til pilotproduktionen, indtil styktallene er store nok til at investere i sprøjtestøbeforme.
Gennem samarbejdet med Teknologisk Institut er Manigrip således gået fra idé til et produktionsklart koncept, som kan masseproduceres med sprøjtestøbning, og hvor både mekanik og elektronik er specificeret og testet - og hele processen tog omkring trekvart år inklusive forbrugertest.
- Samarbejdet med Teknologisk Institut har været rigtig godt. Vi synes det har været dejligt at opleve et engagement deres side, som man faktisk ikke forventer, når man går ind og køber en ydelse fra nogen. Men der har været stor interesse i at udvikle det bedst mulige produkt, og så fra deres side, og det synes vi har været vildt dejligt, konkluderer Henrikke Pedersen, medstifter af Manigrip.
Manigrip lancerer grebsforstørreren, som har fået navnet ‘Wini’, i sommeren 2020, og der er allerede åbnet for bestilling.