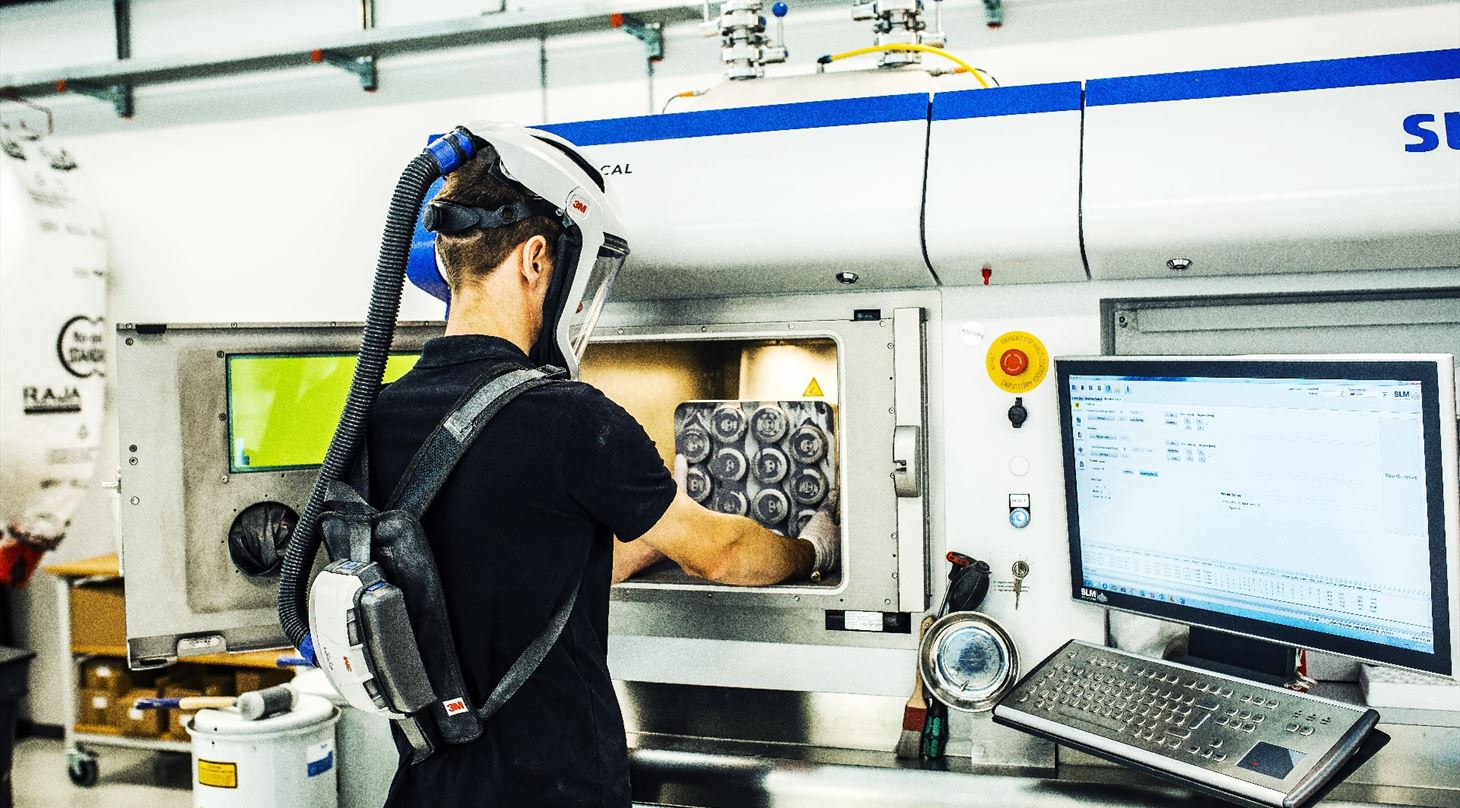
Største danske satsning på metal 3D-print har givet billigere og bedre komponenter
Publiceret den 28. oktober 2021.
For lige knap fire år siden blev AM-LINE 4.0-projektet søsat som den største danske satsning på 3D-print nogensinde. Målet var at skabe et industrielt gennembrud for metal 3D-print i Danmark, og danske industrigiganter som Danfoss og Grundfos har allerede opnået imponerende resultater med teknologien: Med 3D-print kan de fremstille billigere og bedre komponenter – og langt hurtigere end tidligere.
På fire år har store og små virksomheder fået metal 3D-print-teknologien ind under huden: De har sparet tid, materialer og er rustet til fremtidens produktion.
Det er sket via projektet AM-LINE 4.0, der har til formål at skabe et industrielt gennembrud for metal 3D-print i Danmark. AM-LINE 4.0 blev lanceret i 2018 som den største danske satsning på teknologien nogensinde, der skal sikre industrivirksomheder viden og kapacitet til at udnytte det store potentiale i 3D-print af metalemner.
- Med 3D-print får du stor designfrihed, hurtig udvikling og en fleksibel produktion, og det er der mange danske virksomheder, der har fået øjnene op for. I løbet af projektet har vi printet omkring 30.000 metal-emner på de to nye metalprintere, som vi indkøbte i forbindelse med AM-LINE 4.0 – men vi har stadig kapacitet til mere, fortæller Jeppe Byskov, leder af Center for Industriel 3D-print på Teknologisk Institut og projektleder i AM-LINE 4.0.
Danfoss og Grundfos HAR fundet potentialet
For de to kommercielle partnere i projektet – Danfoss og Grundfos – spiller 3D-print en vigtig strategisk rolle, og begge virksomheder har i løbet af de sidste fire år identificeret metalemner i deres produktion, som med fordel kan 3D-printes.
- Vi har enormt mange komponenter, og mange af dem egner sig til 3D-print og kan udnytte den merværdi, som teknologien giver. Samtidig kigger vi mod fremtiden, og her er der en lang række designs, som med fordel kan laves til 3D-print, lyder det fra Werner Stapela, Global Head of Additive Design & Manufacturing.
I projektet har Danfoss og Grundfos udvalgt 31 business cases – både værktøjer og slutkomponenter – som har haft et meget stort potentiale, fx i forhold til reduceret vægt, kortere fremstillingstid og lavere pris. Det resulterer i kortere time-to-market og optimeret produktivitet. Disse komponenter er blevet
3D-printet og testet i projektet med stor gevinst:
Hos Danfoss har man fx 3D-printet et fikstur til trykprøvning af ventiler. Motivationen for at 3D-printe var at reducere vægten og dermed lettere håndteringen, da værktøjet ved brug skal løftes 5-6 gange i timen.
- Ved hjælp af simuleringer har vi reduceret vægten fra 12 kg. til 2,8 kg, fortæller Niklas Franke, Head of Additive Design and Manufacturing, Danfoss Heating og tilføjer, at prisen også fik et nyk nedad: Fra 50.000 kr. til 32.500 kr.
Høj volumen er næste skridt
Næste skridt bliver at gøre metal 3D-print til højvolumenproduktion, og her er Grundfos godt i gang med at vise vejen.
- I takt med at AM er blevet en mere moden produktionsproces til fremstilling af slutkomponenter, ser vi også teknologien som mere end blot en teknologi til fremstilling af prototyper hos Grundfos. Vi ser, at AM bliver en endnu vigtigere teknologi fremadrettet, der skal være med til at sikre vores kunder de bedste og mest pålidelige produkter og løsninger i fremtiden. Vi vil fortsat både udvikle og modne teknologierne for at kunne tilpasse dem til vores behov og her er et naturligt område inden for både polymer og metal 3D-print til højvolumenproduktion og kundespecifikke løsninger, siger Thorsten Brorson Otte, Senior Manager AME COE Additive Manufacturing hos Grundfos.
Stor interesse fra industrien
I forbindelse med AM-LINE-projektet etablerede Teknologisk Institut Center for industriel 3D-print, hvor danske virksomheder har adgang til en komplet produktionslinje og rådgivning fra eksperter inden for industriel 3D-print i metal.
Både store globale virksomheder og SMV’er har fået gavn af centeret, og i projektperioden er der sket en positiv udvikling i brugen af 3D-print hos danske fremstillingsvirksomheder. Ifølge Danmarks Statistik brugte 16 % nemlig teknologien i 2018, mens tallet var steget til 23 % i 2020 – og der forventes yderligere stigninger de kommende år, nu hvor vejen er banet for det industrielle gennembrud.
AM-LINE 4.0 afsluttes ved udgangen af 2021, og for at markere den store indsats, inviterer Teknologisk Institut og MADE – Manufacturing Academy of Denmark til afslutningsevent den 4. november på Teknologisk Institut i Aarhus, hvor alle partnere præsenterer deres arbejde og konkrete resultater i projektet.
At AM-LINE 4.0 afsluttes, betyder dog ikke, at indsatsen stopper, og partnerne vil fortsætte det vigtige arbejde med at udbrede kendskabet til Industriel 3D-print og udrulle teknologien til den danske industri.
Fakta om AM-LINE 4.0
AM-LINE 4.0 er et Grand Solutions projekt støttet af Innovationsfonden sammen med en række førende danske virksomheder og vidensinstitutioner fra ind- og udland. Med et samlet budget på 88 mio. kr. er projektet den største satsning på Industriel 3D-print i Danmark nogensinde, og målet er at sikre, at danske industrivirksomheder får den nødvendige viden og kapacitet til at kunne udnytte det store potentiale i 3D-printproduktion.
I projektperioden har Teknologisk Institut introduceret over 6.000 personer til metal 3D-print via kurser, events, virksomhedsbesøg og webinarer.
Partnere: Grundfos, Danfoss, DTU, Oqton, Scada Minds, Joblife, MADE, TWI, SLM Solutions og Teknologisk Institut.
Yderligere oplysninger
- Centerchef Jeppe Skinnerup Byskov, Teknologisk Institut, mobil 7220 2865, mail: jpbn@teknologisk.dk
- Global Head of Additive Design & Manufacturing, Danfoss Werner Stapela, mail: werner.stapela@danfoss.com
- Senior Manager AME COE Additive Manufacturing, Grundfos, Thorsten Brorson Otte, mobil 2943 4898, mail: totte@grundfos.com