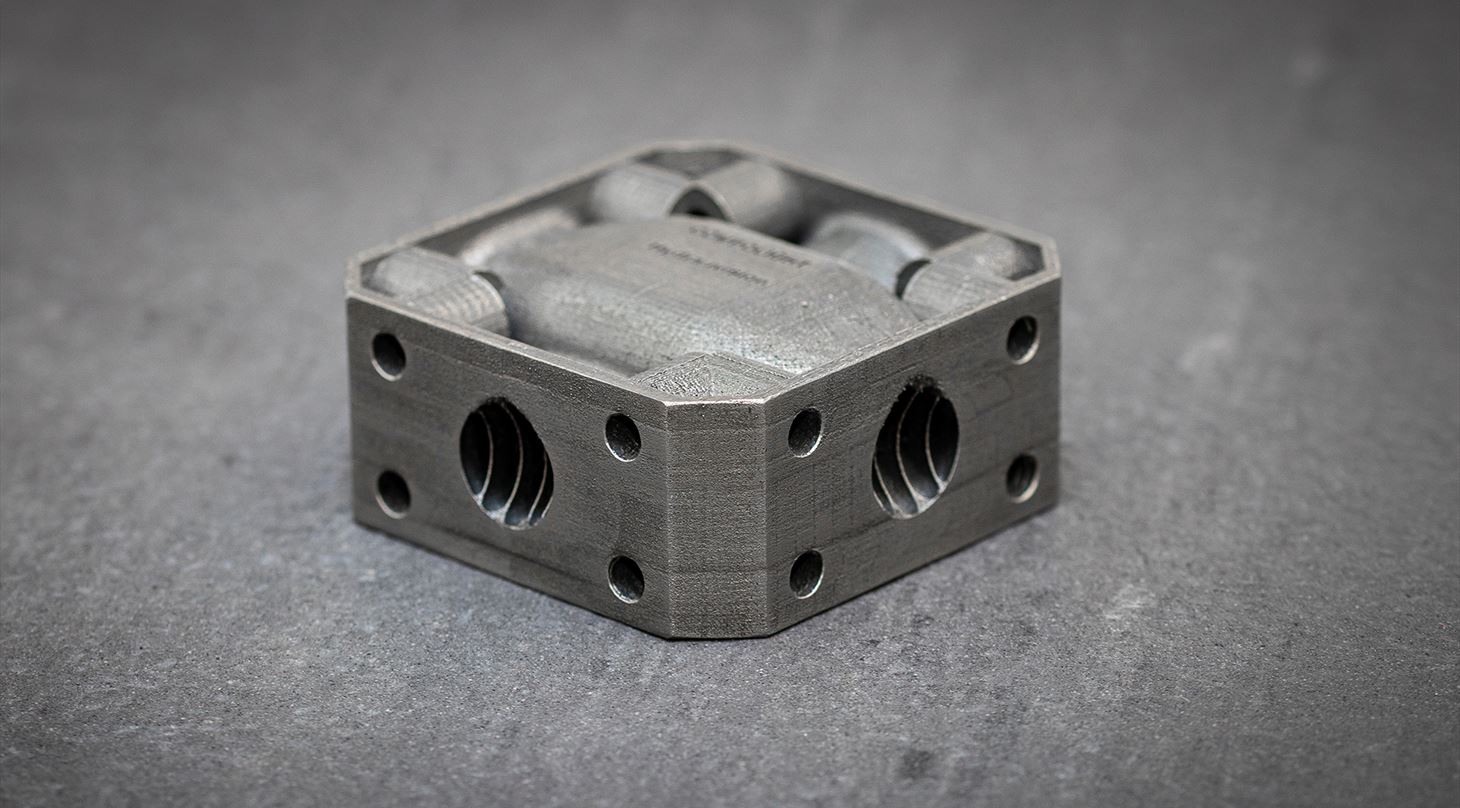
Stor sejr til 3D-print i EU-projekt
Det EU-støttede projekt Compolight, som blev ledet af Center for Industriel Materialeteknologi, viste gode resultater for det hollandske hydraulikfirma Hydrauvision. De nye 3D-printede komponenter forbedrede flowet i de hydrauliske systemer og eliminerede derved store energitab, samtidig med at vægten og størrelsen blev reduceret betydeligt.
Ved hjælp af 3D-print teknologi var den internationale hydraulikvirksomhed Hydrauvision, der holder til i Holland, i stand til at reducere tryktabet med op til 25% sammenlignet med den traditionelle løsning. Virksomheden var en af de 12 deltagere i det europæiske forskningsprojekt ’Compolight’, som blev ledet af Center for Industriel Materialeteknologi på Teknologisk Institut.
Lad os hjælpe dig med 3D-print produktion
- Naturligvis er Hydrauvisions resultater interessante for virksomheden selv, fordi det kan hjælpe med at bringe dem langt foran deres konkurrenter. Men resultaterne er også interessante for danske virksomheder, da de tydeligt viser, hvor store fordele der kan være ved at arbejde med 3D-print. Derudover har både luftfartsindustrien og bilindustrien vist stor interesse for resultaterne, fordi disse industrier har særligt fokus på at reducere vægten og størrelsen på et antal komponenter, siger Olivier Jay, som var sektionsleder ved Teknologisk Institut under projektet.
Han forklarer, at Hydrauvision-casen handlede om at udskifte en traditionelt fremstillet komponent i et hydraulisk system med en 3D-printet komponent.
Reduceret tryktab, lavere vægt og et kompakt design
Traditionelle løsninger har typisk tryktab i et eller andet omfang. Hydrauvisions tryktab opstod på grund af konstruktionen, som groft sagt betød, at to hydrauliske strømme skulle krydse hinanden på meget begrænset plads. Ved hjælp af 3D-print blev der skabt en ny løsning uden rette vinkler og med en meget mere kompleks konstruktion, så der var en uhindret strøm af olie og luft gennem hele systemet.
3D-print har desuden reduceret både vægten og størrelsen på komponenten - fra en størrelse på 230x230x54 mm og en vægt på 20,15 kg til en størrelse på 80x80x50 mm og en vægt på kun 0,95 kg. Faktisk ville det have været muligt at reducere både vægt og størrelse yderligere. Samtidig blev den nye 3D-printede komponent testet til at modstå et tryk på op til 400 bar.
Perspektiverne ved denne udvikling er enorme for Hydrauvision, der arbejder med store fartøjer og meget store hydrauliske systemer. Nu hvor de er i stand til at reducere tryktabet i hele systemet, har de ikke brug for så stort et hydraulisk system som tidligere til at håndtere opgaven. I tilfælde af tryktab skabes der overskydende varme i systemet, som derefter skal afkøles ved hjælp af et kølesystem. Når mængden af varme reduceres, er der behov for et mindre kølesystem - hvilket igen hjælper med at reducere det samlede energiforbrug.
I tillæg til ovenstående løsning re-designede projektet også et endnu større hydraulisk element, der blev brugt i en pumpe til en plast-ekstruderingsmaskine. Her vejede den originale komponent 55 kg, men ved at optimere volumen med komplekse indre kanaler i stedet for blot at bore lige kanaler, formåede projektet at reducere vægten til kun 18 kg.
Fordelen ved 3D-print af komponenter som disse er, at de ikke længere er underlagt de samme geometriske begrænsninger, og derfor har designeren mulighed for frit at optimere komponentens funktion. I dette tilfælde var det et spørgsmål om at optimere tryktabet gennem komponenten ved hjælp af flow-simuleringer.
Optimering af flow i indre kanaler
Ved at udnytte den geometriske frihed ved 3D-print processer er det muligt at bygge komplekse interne kanaler, herunder variable krydsninger samt integration af ribber for at forbedre flowet, varmevekslingen eller andre parametre, samtidig med at komponentens stivhed bevares. 3D-printteknologi kan med fordel anvendes inden for konform køling, hydrauliske dele og mange andre områder.
Formgivningen og dermed ydeevnen af hydrauliske dele er ofte begrænset af, at der bruges traditionelle værktøjer - samt en naturlig konservativ tankegang fra designeren.
Normalt ville man bore to lige kanaler, der mødes et sted inden i blokken. Denne metode er hurtig, billig og kræver kun traditionelle værktøjer. Konsekvensen er dog, at flow-egenskaberne nær hjørnet forringes alvorligt af geometrien. Omvendt giver 3D-print designeren den geometriske frihed til faktisk at optimere komponenten i forhold til dens formål. I dette tilfælde er et lavt tryktab fordelagtigt, og ved hjælp af flow-simuleringer kan kanalens optimale form produceres direkte.
Et stærkt boost
Olivier Jay fremhæver, at Hydrauvision efterfølgende har integreret 3D-print, og at virksomhedens udvikling har fået et markant løft med deltagelsen i Compolight-projektet.
- Derfor vil jeg også benytte lejligheden til at opfordre danske SMV'er til at være opmærksomme på lignende muligheder for at deltage i EU-støttede projekter, der kan give dem et innovativt løft fremover. Compolight-projektet er et godt eksempel herpå. Vi startede projektet i 2008 og afsluttede det i 2011. Projektet, der havde deltagelse af 12 forskellige virksomheder og institutter, arbejdede intenst med at udvikle nye og lettere komponenter, og det er lykkedes over al forventning, konkluderer Olivier Jay.